Robot joint reducer test bed
A robot joint and reducer technology, applied in the field of transmission testing, can solve the problems of low degree of automation, poor adjustability, and few experimental items, and achieve the effects of reducing manual operation, reducing energy consumption and accurate data
- Summary
- Abstract
- Description
- Claims
- Application Information
AI Technical Summary
Problems solved by technology
Method used
Image
Examples
Embodiment Construction
[0030] In this example, see figure 1 , a test bench for a robot joint reducer, comprising: a drive motor 1, a sensor 3, a tested robot joint reducer 5, a loader 6, an output disk 9, a torsion spring 10, a rotation angle device 12, a rotation angle disk 14, and an angle sensor 17. Support frame 18 and control system;
[0031] A sensor 3 is installed between the input end of the tested reducer 5 and the drive motor 1, the controllable steering drive motor 1 is connected to the sensor through the coupling 2, and the sensor 3 is connected to the input of the tested reducer 5 through the coupling 4 The sensor 3 can be a different type of sensor, so as to test different types of data and facilitate the testing of multiple items, and the output end of the tested reducer 5 is connected to the side end surface of the output disc 9 through the mounting hole on it. connected;
[0032] A fixed disk 7 is arranged on the outside of the output disk 9, and a loader 6 is arranged above the f...
PUM
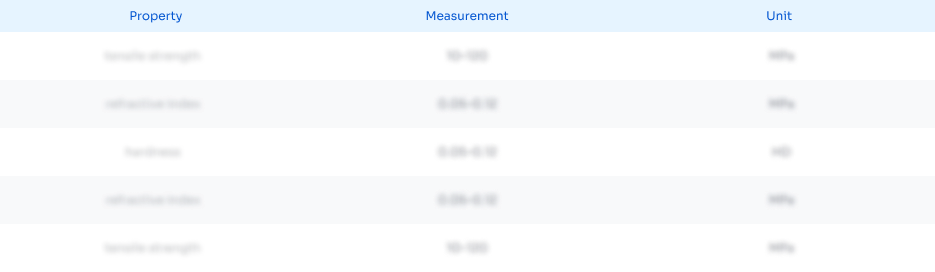
Abstract
Description
Claims
Application Information

- R&D
- Intellectual Property
- Life Sciences
- Materials
- Tech Scout
- Unparalleled Data Quality
- Higher Quality Content
- 60% Fewer Hallucinations
Browse by: Latest US Patents, China's latest patents, Technical Efficacy Thesaurus, Application Domain, Technology Topic, Popular Technical Reports.
© 2025 PatSnap. All rights reserved.Legal|Privacy policy|Modern Slavery Act Transparency Statement|Sitemap|About US| Contact US: help@patsnap.com