Blast furnace screw material distribution correcting method
A cloth and spiral technology is applied in the correction field of the blast furnace bell-type top spiral cloth. , the effect of improving furnace conditions
- Summary
- Abstract
- Description
- Claims
- Application Information
AI Technical Summary
Problems solved by technology
Method used
Examples
Embodiment 1
[0014] For the ore material type O1, the single ring position of the spiral material distribution program originally set by the furnace top distribution program is 9, 8, 7, 6, 5, 4, that is, its X1 is the fourth ring position. The Xj set by the fabric correction program is 2 ring positions higher than X1, that is, it is set as the sixth ring position.
[0015] Under normal circumstances, when the ore material type O1 is distributed, it is executed according to the single ring positions 9, 8, 7, 6, 5, and 4 of the spiral material distribution originally set in the furnace roof distribution program.
[0016] When the weight displayed on the weighing cabinet changes greatly during the fabric making process, manually start the fabric correction program, press the upside-down fabric execution sign button in the spiral fabric list screen, and when the fabric reaches the last fabric ring position X1 (p. 4 ring positions), the material distribution chute will automatically tilt up acc...
Embodiment 2
[0018] For the ore material type O2, the single ring position of the spiral material distribution program originally set by the furnace roof distribution program is 9, 8, 7, 6, 5, that is, its X1 is the fifth ring position. The Xj set by the cloth correction program is the seventh ring position.
[0019] Under normal circumstances, when the ore material is distributed O2, it is executed according to the single-ring positions 9, 8, 7, 6, and 5 of the spiral material distribution program originally set in the furnace roof distribution program.
[0020] When the weight displayed on the weighing cabinet changes greatly during the fabric making process, manually start the fabric correction program, press the upside-down fabric execution sign button in the spiral fabric list screen, and when the fabric reaches the last fabric ring position X1 (p. 5 ring positions), the material distribution chute will automatically tilt up according to the tilting angle of the searched spiral materi...
PUM
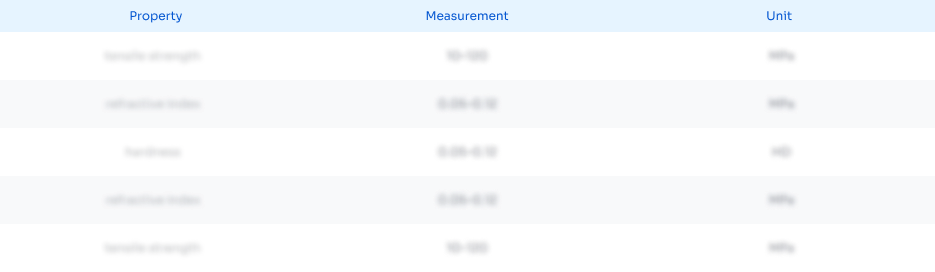
Abstract
Description
Claims
Application Information

- R&D
- Intellectual Property
- Life Sciences
- Materials
- Tech Scout
- Unparalleled Data Quality
- Higher Quality Content
- 60% Fewer Hallucinations
Browse by: Latest US Patents, China's latest patents, Technical Efficacy Thesaurus, Application Domain, Technology Topic, Popular Technical Reports.
© 2025 PatSnap. All rights reserved.Legal|Privacy policy|Modern Slavery Act Transparency Statement|Sitemap|About US| Contact US: help@patsnap.com