Robot calibration method based on measuring head
A calibration method and robot technology, applied in the field of robot calibration, can solve problems such as expensive data measurement and complex calibration models, and achieve the effects of improving absolute positioning accuracy, obvious calibration effect, and low cost
- Summary
- Abstract
- Description
- Claims
- Application Information
AI Technical Summary
Problems solved by technology
Method used
Image
Examples
Embodiment Construction
[0031] refer to figure 1 , 2 , 3, 4, a method for calibration of a robot based on a measuring head, comprising the following steps:
[0032] A. Establish robot kinematics model
[0033] Establishing the robot kinematics model is the basis for analyzing the performance of the robot, and the robot motion model is established by the traditional D-H method. The D-H method is to use four parameters θ, d, α, a to represent the homogeneous transformation relationship between the robot linkages, θ represents the robot joint x i-1 and x i Angle around the z axis; d stands for x i-1 and x i The distance to translate along the z-axis; α represents z i-1 and z i Rotation angle around the x-axis; a represents z i-1 and z i The distance translated along the x-axis transforms the link coordinate system i to the homogeneous transformation matrix A of the link coordinate system i-1 i for:
[0034] A i =Rot(X,α i-1 )Trans(X,a i-1 )Rot(Z,θ i )Trans(Z,d i )
[0035] Then the tota...
PUM
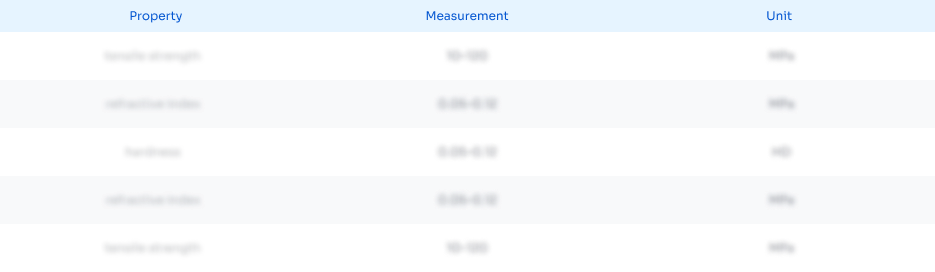
Abstract
Description
Claims
Application Information

- Generate Ideas
- Intellectual Property
- Life Sciences
- Materials
- Tech Scout
- Unparalleled Data Quality
- Higher Quality Content
- 60% Fewer Hallucinations
Browse by: Latest US Patents, China's latest patents, Technical Efficacy Thesaurus, Application Domain, Technology Topic, Popular Technical Reports.
© 2025 PatSnap. All rights reserved.Legal|Privacy policy|Modern Slavery Act Transparency Statement|Sitemap|About US| Contact US: help@patsnap.com