New technology for clean production of chitosan and carboxymethyl chitosan by using crustacean shell raw materials
A carboxymethyl chitosan and crustacean technology, which is applied in the field of biomass utilization and natural product modification, can solve the problems of high acid-base and energy consumption, waste of biological calcium resources, and high cost of chitin extraction, and achieves improved conversion. rate, enhance nucleophilic ability, overcome the effect of "shielding" effect
- Summary
- Abstract
- Description
- Claims
- Application Information
AI Technical Summary
Problems solved by technology
Method used
Image
Examples
Embodiment 1
[0039] Add solid sodium hydroxide to the isopropanol-water mixing system, stir at 60°C for a period of time to form a paste liquid, then weigh the shrimp shell powder and add them to the above mixture, stir for 3 hours, the chitin is fully deacetylated, and the solid Add water and wash to obtain chitosan and calcium carbonate mixture, then dissolve chitosan and calcium carbonate with hydrochloric acid, reverse precipitate chitosan with ethanol, wash repeatedly with 70% alcohol aqueous solution to remove calcium chloride to obtain pure chitosan. The degree of deacetylation was determined by acid-base titration. See Table 2, Table 3, and Table 4 for relevant experimental results under different m (shrimp shell powder): m (sodium hydroxide), water content, and temperature.
[0040] The effect of the amount of epidihydric sodium hydroxide on the degree of deacetylation of chitin
[0041]
[0042] Table 3 The effect of water content on the degree of deacetylation of chitin
[...
Embodiment 2
[0048] Add 15g of sodium hydroxide solid to 100ml of isopropanol-water mixed system containing 10% water, stir at 60°C for a period of time to form a paste liquid, then weigh 45g of decalcified shrimp shell powder and add to the above mixture, 60 Under electric stirring at ℃ for 3h, chitin is fully deacetylated. Chloroacetic acid was added in 3 to 7 times respectively, and chitosan was carboxymethylated for 3 hours. The solid obtained by filtration and separation was washed with 70% ethanol solution to obtain a mixture of carboxymethyl chitosan and calcium carbonate. The mixture was dissolved in water, and the supernatant obtained by centrifugation was added with 5 times the volume of ethanol to precipitate, and then the precipitate was washed with 80% ethanol three times, dried to obtain pure carboxymethyl chitosan, and the carboxylation degree of the product was determined by potentiometric titration. different m (虾壳粉) :m (-氯乙酸) 1. See Table 5 and Table 6 for the relevant...
Embodiment 3
[0054] Add 30g of sodium hydroxide solid to the 100ml ethanol-water mixed system containing 10% water and stir evenly, then weigh 45g of decalcified shrimp shell powder and add it to the above mixture, stir and reflux at 80°C for 3 hours to fully deacetylate chitin . Then add monochloroacetic acid in 3 to 7 times, and carboxymethylate chitosan for 3 hours. The product was washed with an aqueous alcohol solution and dried to obtain 28 g of the mixture. Water was added to dissolve and precipitate 21 g of calcium carbonate, and the solution was reverse-precipitated with ethanol to obtain 6.8 g of carboxymethyl chitosan. The deacetylation degree of carboxymethyl chitosan product is 0.72, and the carboxylation degree is 0.69.
PUM
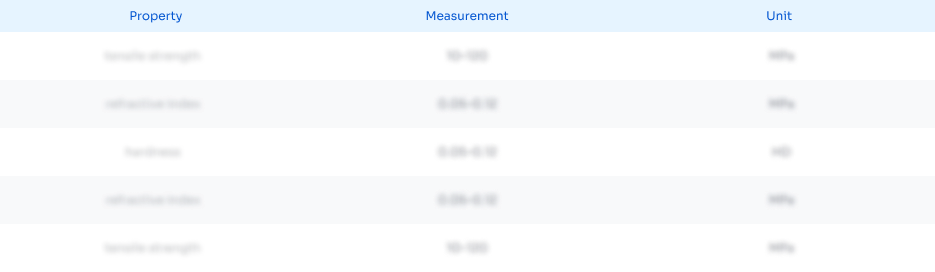
Abstract
Description
Claims
Application Information

- R&D
- Intellectual Property
- Life Sciences
- Materials
- Tech Scout
- Unparalleled Data Quality
- Higher Quality Content
- 60% Fewer Hallucinations
Browse by: Latest US Patents, China's latest patents, Technical Efficacy Thesaurus, Application Domain, Technology Topic, Popular Technical Reports.
© 2025 PatSnap. All rights reserved.Legal|Privacy policy|Modern Slavery Act Transparency Statement|Sitemap|About US| Contact US: help@patsnap.com