Robot gripper driven by gear
A robot gripper and gear transmission technology, applied in the direction of manipulators, program-controlled manipulators, chucks, etc., can solve the problems of not being able to further improve production efficiency, narrow the scope of application of robot grippers, and reduce the versatility of robot grippers, etc., and achieve simple structure , stable clamping, fast grabbing effect
- Summary
- Abstract
- Description
- Claims
- Application Information
AI Technical Summary
Problems solved by technology
Method used
Image
Examples
Embodiment 1
[0025] In this embodiment, four movable rods are provided as an example to describe the following.
[0026] Such as figure 1 and figure 2 Shown, the robot gripper of the gear transmission of the present invention is connected with the robot movable section; It comprises the support 1 that is connected with the robot movable section, the gear transmission set on the support 1, the rotary cylinder 2 (such as 180 degree rotating cylinder) and four movable rods 3; wherein, the movable rod 3 is connected with the gear transmission, and the gear transmission both sides are all provided with two movable rods 3, and each movable rod 3 can open and close the movement. The movable rods 3 of the present invention are evenly arranged on both sides of the gear transmission device, and the movable rods 3 on both sides are mirror images, and the inner side of each movable rod 3 is set as an arc surface, which can further ensure the stable clamping of the workpiece.
[0027] The gear trans...
Embodiment 2
[0032] The only difference between this embodiment and Embodiment 1 is that the movable rods can be set to be multiple, and the multiple movable rods are evenly distributed on both sides of the gear transmission, so that the grasping area of the gripper can be increased, and it is suitable for larger Workpieces are quickly picked up and clamped smoothly.
[0033] Other structures of this embodiment are consistent with Embodiment 1.
PUM
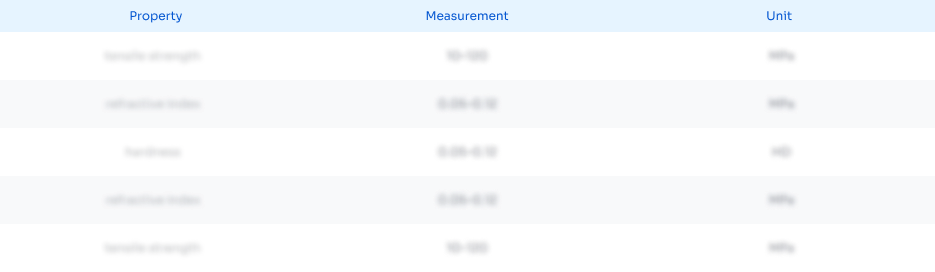
Abstract
Description
Claims
Application Information

- Generate Ideas
- Intellectual Property
- Life Sciences
- Materials
- Tech Scout
- Unparalleled Data Quality
- Higher Quality Content
- 60% Fewer Hallucinations
Browse by: Latest US Patents, China's latest patents, Technical Efficacy Thesaurus, Application Domain, Technology Topic, Popular Technical Reports.
© 2025 PatSnap. All rights reserved.Legal|Privacy policy|Modern Slavery Act Transparency Statement|Sitemap|About US| Contact US: help@patsnap.com