Regenerated rubber matrix based combined damping plate and manufacturing method
A technology of recycled rubber and composite damping, applied to springs made of plastic materials, springs/shock absorbers, mechanical equipment, etc., can solve problems such as low sound insulation, troublesome painting of asbestos paint, sound insulation failure, etc., to achieve Reduce material costs, improve sound insulation, and reduce pollution
- Summary
- Abstract
- Description
- Claims
- Application Information
AI Technical Summary
Problems solved by technology
Method used
Image
Examples
Embodiment Construction
[0019] The embodiments of the present invention will be described in detail below with reference to the accompanying drawings, but the present invention can be implemented in many different ways defined and covered by the claims.
[0020] The composite damping plate includes a bottom layer and a damping layer. The damping layer is divided into a free damping layer and a constrained damping layer, such as figure 1 As shown, the free damping layer structure includes a bottom layer and a damping layer. The bottom layer is a thick steel plate 1, the damping layer is modified reclaimed rubber 3, and the thick steel plate 1 is stamped with convex grooves of different shapes to form reinforcing ribs. To increase the rigidity of the steel plate, in order to facilitate the adhesion of the thick steel plate 1 and the modified recycled rubber 3, a thin layer of Chemlock glue 2 is applied on the joint surface of the thick steel plate 1 and the modified recycled rubber 3.
[0021] Such as figu...
PUM
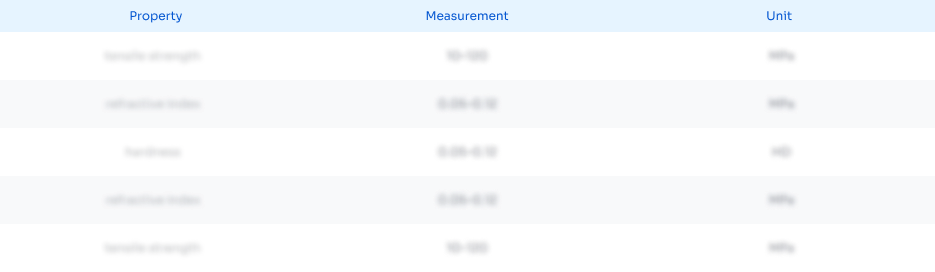
Abstract
Description
Claims
Application Information

- R&D
- Intellectual Property
- Life Sciences
- Materials
- Tech Scout
- Unparalleled Data Quality
- Higher Quality Content
- 60% Fewer Hallucinations
Browse by: Latest US Patents, China's latest patents, Technical Efficacy Thesaurus, Application Domain, Technology Topic, Popular Technical Reports.
© 2025 PatSnap. All rights reserved.Legal|Privacy policy|Modern Slavery Act Transparency Statement|Sitemap|About US| Contact US: help@patsnap.com