Production method of flame-retardant modified wood
A production method and wood technology, applied in wood treatment, wood impregnation, wood impregnation and other directions, can solve the problems of poor mechanical properties of wood, insignificant fire retardant effect of wood, complicated modification treatment process, etc., and achieve excellent flame retardant properties. The effect of improving the physical and mechanical properties and simplifying the process
- Summary
- Abstract
- Description
- Claims
- Application Information
AI Technical Summary
Problems solved by technology
Method used
Examples
Embodiment 1
[0019] Preparation of flame retardant (by weight): 1. Mix 25 parts of diammonium hydrogen phosphate, 10 parts of pentaerythritol, 8 parts of zinc borate and 50 parts of water, and stir to obtain final product; 2. Prepare modified urea-formaldehyde Resin solution (by weight): 150 parts of formaldehyde, 62 parts of urea, 8 parts of thiourea and 350 parts of water are mixed together, stirred evenly, to obtain final product; 3. Add 21 parts by weight of flame retardant to modified urea-formaldehyde resin After dissolving completely in 70 parts by weight of the liquid, the impregnating liquid is obtained; four, the impregnating treatment of poplar wood: the wood is put into a vacuum pressurized tank, and first vacuumed so that the relative vacuum degree in the vacuum pressurized tank reaches-0.085MPa, Keep the vacuum pump off after 30 minutes, and import the wood impregnating solution obtained in step 1 at the same time until the relative vacuum in the vacuum pressurized tank is 1.3...
Embodiment 2
[0022] The only difference between this embodiment and Example 1 is: the parts by weight of each component of the flame retardant are as follows: 20 parts of diammonium hydrogen phosphate, 15 parts of pentaerythritol, 10 parts of zinc borate and 70 parts of water, other steps and parameters and implementation Example 1 is exactly the same.
[0023] The flame-retardant modified poplar prepared in this example has a final weight gain of 25% and a dimensional stability of 20%. Its oxygen index was tested according to GB / T2406-93, and it was measured according to the wood hardness test method of GB 1941-1991 Hardness, measured water absorption according to GB 12626.8-1990, it can be seen that the prepared flame-retardant modified poplar oxygen index increased by 35%, surface hardness increased by 80%, and water absorption decreased by 65%.
Embodiment 3
[0025] The only difference between this embodiment and Example 1 is: the parts by weight of each component of the flame retardant are as follows: 35 parts of diammonium hydrogen phosphate, 20 parts of pentaerythritol, 15 parts of zinc borate and 85 parts of water, other steps and parameters and implementation Example 1 is exactly the same.
[0026] The flame-retardant modified poplar prepared in this example has a final weight gain rate of 40% and a dimensional stability of 40%. The oxygen index was tested according to GB / T2406-93, and the hardness was measured according to the wood hardness test method GB 1941-1991 , according to GB 12626.8-1990 to measure the water absorption, it can be known that the oxygen index of the prepared flame-retardant modified poplar has increased by 60%, the surface hardness has increased by 87%, and the water absorption has decreased by 75%.
PUM
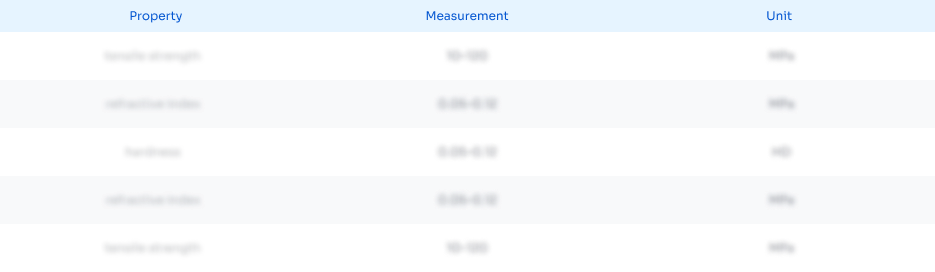
Abstract
Description
Claims
Application Information

- R&D
- Intellectual Property
- Life Sciences
- Materials
- Tech Scout
- Unparalleled Data Quality
- Higher Quality Content
- 60% Fewer Hallucinations
Browse by: Latest US Patents, China's latest patents, Technical Efficacy Thesaurus, Application Domain, Technology Topic, Popular Technical Reports.
© 2025 PatSnap. All rights reserved.Legal|Privacy policy|Modern Slavery Act Transparency Statement|Sitemap|About US| Contact US: help@patsnap.com