Centrifugal casting process of high-performance engine alloy cylinder sleeve
A technology of centrifugal casting and engine, which is applied in the field of casting, can solve the problems that the precision of castings cannot be effectively guaranteed, the hardness and toughness are not enough, and the casting process is cumbersome, so as to achieve high raw material utilization, improve production efficiency, and optimize mold design.
- Summary
- Abstract
- Description
- Claims
- Application Information
AI Technical Summary
Problems solved by technology
Method used
Examples
Embodiment
[0017] The high-performance engine alloy cylinder liner centrifugal casting process of the present embodiment comprises the following steps:
[0018] (1) Optimizing the design of the machining allowance of the blank to improve the uniformity of the section structure of the formed part. The machining allowance of the outer circle of the blank is 3 mm on one side, and the inner cavity allowance is 3.5 mm on one side;
[0019] (2) On the basis of meeting the basic chemical composition of the material in terms of weight percentage: C 3.5, Si 2.2, Mn 0.8, P 0.4, S 0.12, Cr 0.4, Cu 0.3, and the balance is iron, add 0.15 wt.% tin alloying;
[0020] (3) Inoculation: the total inoculation amount is controlled at 0.5wt.%, among which, the inoculation amount of ladle inoculation is equal to 0.1%;
[0021] (4) When pouring, the thickness of the coating in the inner cavity of the mold is controlled at 1.2 mm;
[0022] (5) The interval between pouring and water release is 20 seconds; the ...
PUM
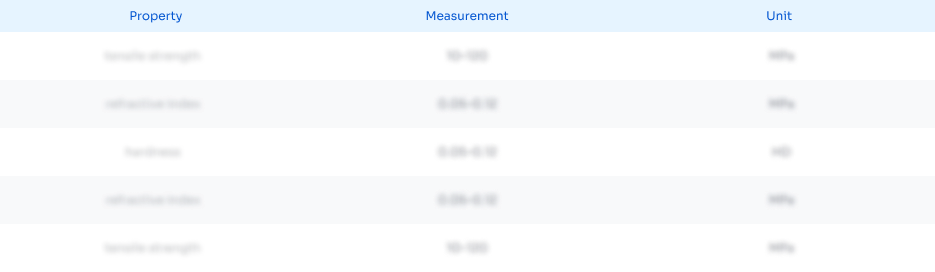
Abstract
Description
Claims
Application Information

- R&D
- Intellectual Property
- Life Sciences
- Materials
- Tech Scout
- Unparalleled Data Quality
- Higher Quality Content
- 60% Fewer Hallucinations
Browse by: Latest US Patents, China's latest patents, Technical Efficacy Thesaurus, Application Domain, Technology Topic, Popular Technical Reports.
© 2025 PatSnap. All rights reserved.Legal|Privacy policy|Modern Slavery Act Transparency Statement|Sitemap|About US| Contact US: help@patsnap.com