Hydraulic pressure control device for machinery
A technology for working machinery and control devices, which is applied to fluid pressure actuation devices, mechanical equipment, mechanically driven excavators/dredgers, etc., can solve problems such as energy loss, reduce overflow flow, etc. The effect of improving energy efficiency and improving operational performance
- Summary
- Abstract
- Description
- Claims
- Application Information
AI Technical Summary
Problems solved by technology
Method used
Image
Examples
no. 1 Embodiment approach
[0054] ~The first embodiment~
[0055] figure 2 It is a figure which shows a part of the hydraulic pressure control apparatus in 1st Embodiment of this invention.
[0056] The hydraulic control device of the present embodiment has: a prime mover (such as a diesel engine) 1; a variable displacement hydraulic pump 2 driven by the prime mover 1; driven by oil; directional control valve 3, which controls the flow of hydraulic oil supplied from hydraulic pump 2 to hydraulic actuator 4; operating lever device 5, which is used for the operator to input operation instructions; main relief valve 8, which is connected with the hydraulic pressure The pump discharge oil passage 7 connected to the pump 2 and the directional control valve 3 is connected, and the upper limit of the pressure of the pump discharge oil passage 7 (discharge pressure of the hydraulic pump 2) is specified; And the main relief valve 8 and other connections.
[0057] The hydraulic pump 2 is, for example, a varia...
no. 2 Embodiment approach
[0083] ~Second Embodiment~
[0084] Figure 6 It is a figure which shows the control logic of the controller of the hydraulic pressure control apparatus in 2nd Embodiment of this invention. In the figure, the same reference numerals are attached to the same elements as those of the first embodiment, and description thereof will be omitted.
[0085] Figure 6 In this embodiment, the controller 6A is image 3 In addition to the shown configuration, the pump power upper limit setting device 41 sets a power limit value Pwr_ref for limiting the amount of absorbed power of the hydraulic pump 2; a flow rate correction unit 42 (flow rate limit value correction unit) , which is obtained by dividing the power limit value Pwr_ref set by the pump power upper limit setting device 41 by the discharge pressure (current pressure) of the hydraulic pump 2 detected by the pressure detector 21 and multiplying it by the correction coefficient K2, and Calculate the pump flow upper limit value; ...
no. 3 Embodiment approach
[0097] ~Third Embodiment~
[0098] Figure 10 It is a figure which shows the structure of the pump control apparatus of the hydraulic pressure control apparatus in 3rd Embodiment of this invention, and the control logic of a controller. In the figure, the same reference numerals are attached to the same elements as those of the first embodiment, and description thereof will be omitted.
[0099] In the first embodiment, the controller 6 has all the functions up to the determination of the target tilting amount of the hydraulic pump 2 and these functions are executed by software, so that the mechanical regulator 2 a has the function determined by the controller 6 . However, in this embodiment, the controller 6B has the functions of the target pump pressure setting unit 32 and the pump flow rate upper limit setting unit 33, and the mechanical regulator 2aA has the functions of the other functions. Processing function (feedback subtraction unit 34, control amount calculation uni...
PUM
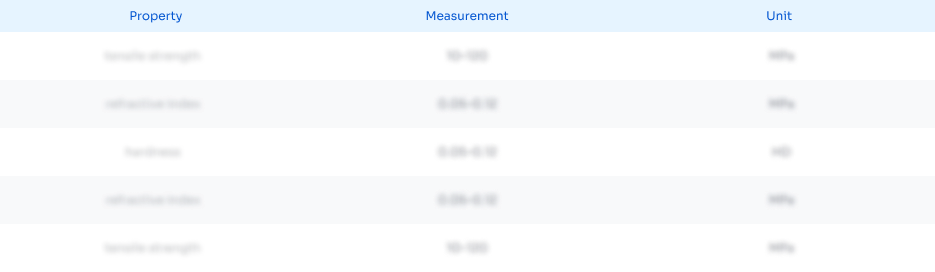
Abstract
Description
Claims
Application Information

- Generate Ideas
- Intellectual Property
- Life Sciences
- Materials
- Tech Scout
- Unparalleled Data Quality
- Higher Quality Content
- 60% Fewer Hallucinations
Browse by: Latest US Patents, China's latest patents, Technical Efficacy Thesaurus, Application Domain, Technology Topic, Popular Technical Reports.
© 2025 PatSnap. All rights reserved.Legal|Privacy policy|Modern Slavery Act Transparency Statement|Sitemap|About US| Contact US: help@patsnap.com