Force effect tester
A tester and force effect technology, which is applied in the field of testers for measuring the overall force effect of motors and propellers, can solve problems such as the difficulty in accurately measuring the force effect parameters of electric aircraft, affecting the signal collection of pressure sensors, and the difficulty in obtaining pressure values for pressure sensors. To achieve the effect of firm structure, elimination of influence and wide dynamic range
- Summary
- Abstract
- Description
- Claims
- Application Information
AI Technical Summary
Problems solved by technology
Method used
Image
Examples
Embodiment Construction
[0014] The present invention will be further described in detail below with reference to the drawings and embodiments:
[0015] Such as figure 1 As shown, the present invention discloses a force effect tester adopting a dual slide rail design. Two symmetrical slide rails 3 are arranged on the base 2, and the slide end 4 is fixed to the symmetrical slide rail 3. The motor mounting frame 6 is fixedly installed on the upper side, and the tensile tester 1 and the sliding end are fixedly connected by bolts or the like. The motor mounting frame 6 can be adapted to install different types of batteries, ESCs, motors and propellers. A test circuit board 5 is installed on the motor mounting frame 6, and the test circuit board 5 has an on-board main control single-chip. Connect the battery to the input end of the test circuit board, connect the power supply line and control line of the ESC to the output end of the test circuit board 5, connect the output end of the ESC to the motor, and f...
PUM
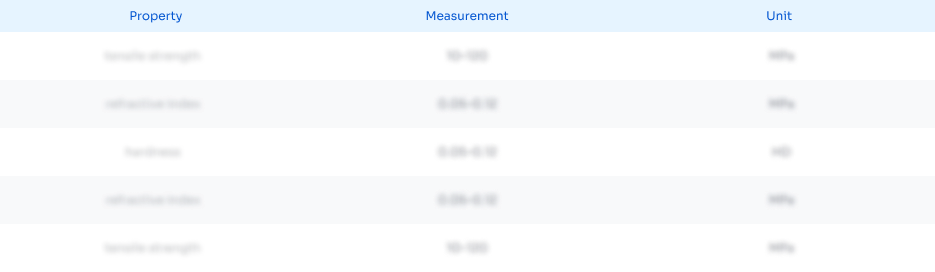
Abstract
Description
Claims
Application Information

- Generate Ideas
- Intellectual Property
- Life Sciences
- Materials
- Tech Scout
- Unparalleled Data Quality
- Higher Quality Content
- 60% Fewer Hallucinations
Browse by: Latest US Patents, China's latest patents, Technical Efficacy Thesaurus, Application Domain, Technology Topic, Popular Technical Reports.
© 2025 PatSnap. All rights reserved.Legal|Privacy policy|Modern Slavery Act Transparency Statement|Sitemap|About US| Contact US: help@patsnap.com