Low-silicon molten iron blowing method
A technology in the early stage of molten iron and blowing, which is applied in the manufacture of converters, etc., can solve the problems of complex silica composition, expensive ferrosilicon, and long melting time, and achieve simple silica composition, improved slagging effect, and short melting time.
- Summary
- Abstract
- Description
- Claims
- Application Information
AI Technical Summary
Problems solved by technology
Method used
Image
Examples
Embodiment 1
[0022] During the 150-ton converter smelting process, the temperature of the molten iron is 1312°C, the silicon content of the molten iron is 0.35% (mass fraction), and the content of phosphorus in the molten iron is 0.14% (mass fraction). The phosphorus content of the finished smelted steel is required to be <0.02% (mass fraction).
[0023] The temperature of molten iron entering the converter is relatively low, and no iron ore is added before blowing.
[0024] Add the first batch of high SiO to the converter at the early stage of blowing to 60s 2 336kg of iron ore is used to promote slag melting. After adding ore, the gun position is reduced from 2210mm to 1990mm, which is 220mm lower, so as to prevent the early splashing caused by the high FeO content of slag after adding ore.
[0025] When blowing reaches 474 seconds, add 426kg of ore to prevent the slag from being excessively dry.
[0026] 424kg and 534kg of ore were added to the blowing until 520 seconds and 572 second...
Embodiment 2
[0029] During the 150-ton converter smelting process, the temperature of the molten iron is 1362°C, the silicon content of the molten iron is 0.35% (mass fraction), and the content of phosphorus in the molten iron is 0.14% (mass fraction). The phosphorus content of the finished smelted steel is required to be <0.02% (mass fraction).
[0030] The molten iron into the converter is higher than 1350℃, 672kg iron ore is added before blowing, and the gun position is lowered by 120mm after adding iron ore.
[0031] Add the first batch of high SiO to the converter at the early stage of blowing to 70s 2 360kg of iron ore is used to promote slag melting. After adding the ore, the gun position is reduced from 2210mm to 1990mm, which is 220mm lower, so as to prevent the early splashing caused by the high FeO content of the slag after the ore is added.
[0032] When blowing reaches 467 seconds, 412kg of ore is added to prevent excessive re-drying of slag, and the gun position is lowered b...
Embodiment 3
[0036] During the 150-ton converter smelting process, the temperature of the molten iron is 1375°C, the silicon content of the molten iron is 0.36% (mass fraction), and the content of phosphorus in the molten iron is 0.15% (mass fraction). The phosphorus content of the finished smelted steel is required to be <0.02% (mass fraction).
[0037] The molten iron into the converter is higher than 1350℃, 850kg iron ore is added before blowing, and the gun position is lowered by 200mm after adding iron ore.
[0038] Add the first batch of high SiO to the converter at the early stage of blowing to 60s 2 310kg of iron ore is used to promote slag melting. After adding the ore, the gun position is reduced from 2210mm to 2080mm, which is 130mm lower, so as to prevent the early splashing caused by the high content of FeO in the slag after the ore is added.
[0039] When blowing reaches 470 seconds, 405kg of ore is added to prevent the slag from excessive re-drying, and the gun position is ...
PUM
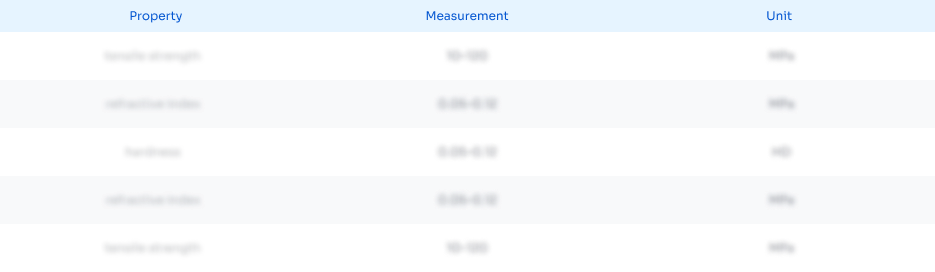
Abstract
Description
Claims
Application Information

- R&D
- Intellectual Property
- Life Sciences
- Materials
- Tech Scout
- Unparalleled Data Quality
- Higher Quality Content
- 60% Fewer Hallucinations
Browse by: Latest US Patents, China's latest patents, Technical Efficacy Thesaurus, Application Domain, Technology Topic, Popular Technical Reports.
© 2025 PatSnap. All rights reserved.Legal|Privacy policy|Modern Slavery Act Transparency Statement|Sitemap|About US| Contact US: help@patsnap.com