Selective compliance assembly robot
A technology of horizontal multi-joint, mechanical arm, applied in the direction of manipulator, program-controlled manipulator, mechanical equipment, etc., can solve the problems of reducing the accuracy of shaft position control, unstable transmission effect, and difficult to replace parts, etc.
- Summary
- Abstract
- Description
- Claims
- Application Information
AI Technical Summary
Problems solved by technology
Method used
Image
Examples
Embodiment Construction
[0014] Please refer to the figures, the horizontal multi-joint mechanical arm 10 provided by a preferred embodiment of the present invention includes a base 20, a first cantilever 30, a second cantilever 40, a rod-shaped linear motor (shaft motor) 50, three Rotary motors 60, 70, 80, and a sleeve 90.
[0015] One end of the first cantilever 30 is arranged on the base 20 , the rotary motor 60 is arranged in the base 20 , and a rotating shaft (not shown in the figure) protrudes upwards, and the rotating shaft is connected with the first cantilever 30 , and can drive the first suspension arm 30 to rotate relative to the base 20 around a first imaginary axis L1.
[0016] One end of the second cantilever 40 is arranged on the other end of the first cantilever 30, the rotary motor 70 is arranged in the second cantilever 40, and protrudes downward from a rotating shaft (not shown in the figure), the rotating shaft Connected with the first cantilever 30; thus, the rotation motor 70 ca...
PUM
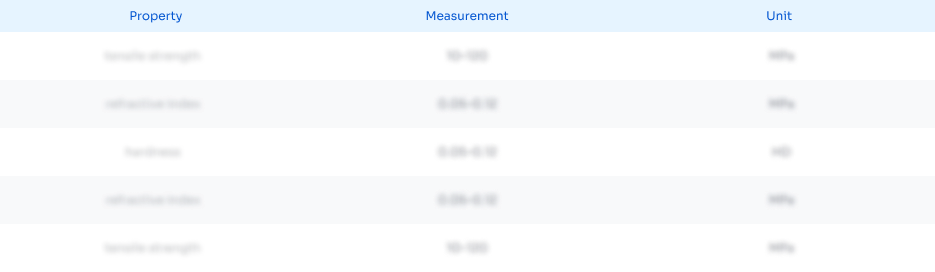
Abstract
Description
Claims
Application Information

- R&D Engineer
- R&D Manager
- IP Professional
- Industry Leading Data Capabilities
- Powerful AI technology
- Patent DNA Extraction
Browse by: Latest US Patents, China's latest patents, Technical Efficacy Thesaurus, Application Domain, Technology Topic, Popular Technical Reports.
© 2024 PatSnap. All rights reserved.Legal|Privacy policy|Modern Slavery Act Transparency Statement|Sitemap|About US| Contact US: help@patsnap.com