Cast sand core for cylinder cover of diesel engine
A diesel engine and foundry sand technology, which is applied to casting molding equipment, molds, cores, etc., can solve the problems of complex sand core floating, long manufacturing cycle, and mold change, so as to achieve no need for mold investment, short development cycle, and low casting cost. low effect
- Summary
- Abstract
- Description
- Claims
- Application Information
AI Technical Summary
Problems solved by technology
Method used
Image
Examples
Embodiment Construction
[0023] The specific embodiments of the present invention will be described in detail below in conjunction with the accompanying drawings, but it should be understood that the protection scope of the present invention is not limited by the specific embodiments.
[0024] Unless expressly stated otherwise, throughout the specification and claims, the term "comprise" or variations thereof such as "includes" or "includes" and the like will be understood to include the stated elements or constituents, and not Other elements or other components are not excluded.
[0025] Such as figure 1 As shown, the casting sand core of the diesel engine cylinder head according to the specific embodiment of the present invention specifically includes: a composite integral sand core 1 , a chassis core 2 , an upper cover disc core 3 and a pouring system auxiliary core 4 . Wherein, the chassis core 2 is only a cavity for accommodating the composite monolithic sand core 1 and a part of the casting sha...
PUM
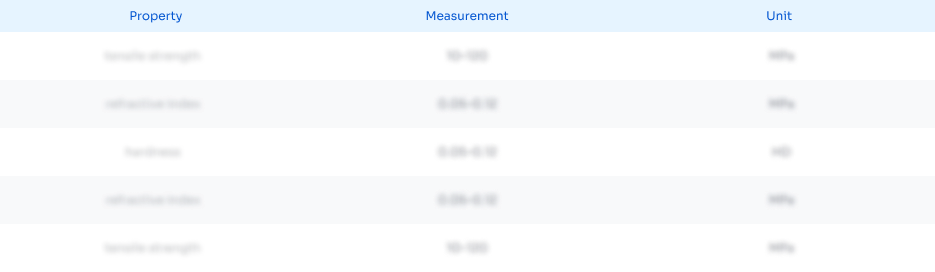
Abstract
Description
Claims
Application Information

- R&D
- Intellectual Property
- Life Sciences
- Materials
- Tech Scout
- Unparalleled Data Quality
- Higher Quality Content
- 60% Fewer Hallucinations
Browse by: Latest US Patents, China's latest patents, Technical Efficacy Thesaurus, Application Domain, Technology Topic, Popular Technical Reports.
© 2025 PatSnap. All rights reserved.Legal|Privacy policy|Modern Slavery Act Transparency Statement|Sitemap|About US| Contact US: help@patsnap.com