Gas spring mounting reinforcement plate structure and method for assembling gas spring mounting reinforcement plate
A technology of gas springs and reinforcing plates, which is applied in the direction of upper structure, upper structure sub-assembly, elastic suspension, etc., can solve problems such as unfavorable weight reduction of the vehicle body, weight increase of the vehicle body, and cracking of solder joints at the installation point of the gas spring, and achieve reliable solutions Durability issues, the effect of improving stiffness
- Summary
- Abstract
- Description
- Claims
- Application Information
AI Technical Summary
Problems solved by technology
Method used
Image
Examples
Embodiment Construction
[0028] The present invention will be further described below in conjunction with the accompanying drawings and specific embodiments.
[0029] Figure 4 to Figure 12 The reference numerals in the figure are: side wall outer panel 1; C-pillar outer reinforcement plate 2; flow tank 3; gas spring installation reinforcement plate 4; gas spring installation nut 5; side wall inner panel 6; top cover rear beam 7; Laminate solder joints 8; three-layer board solder joints 9.
[0030] like Figure 4 to Figure 12 As shown, a gas spring installation reinforcement plate structure includes a rear wheel house assembly, a side wall outer panel 1, a running water tank 3 and a top cover rear beam 7, and the rear wheel house assembly is connected to the side wall outer panel respectively 1. The running water tank 3 and the top cover rear beam 7 are welded into a body in white. The rear wheel house assembly includes the C-pillar outer reinforcement plate 2, the gas spring installation reinforcem...
PUM
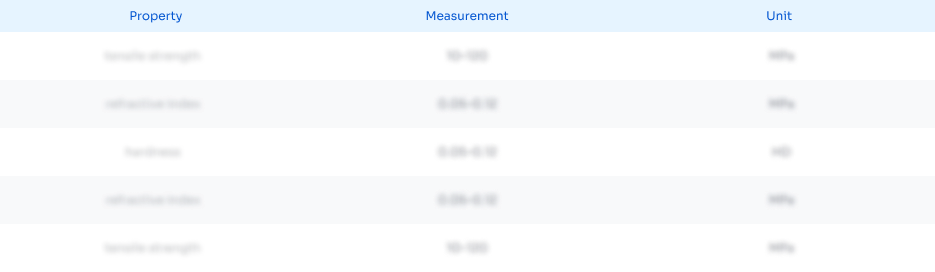
Abstract
Description
Claims
Application Information

- Generate Ideas
- Intellectual Property
- Life Sciences
- Materials
- Tech Scout
- Unparalleled Data Quality
- Higher Quality Content
- 60% Fewer Hallucinations
Browse by: Latest US Patents, China's latest patents, Technical Efficacy Thesaurus, Application Domain, Technology Topic, Popular Technical Reports.
© 2025 PatSnap. All rights reserved.Legal|Privacy policy|Modern Slavery Act Transparency Statement|Sitemap|About US| Contact US: help@patsnap.com