Elevator control device
An elevator control device and elevator system technology, applied in the field of elevator control devices, can solve problems such as lack of clear and accurate calculation means, difficulty in implementation, and difficulty in suppressing or eliminating
- Summary
- Abstract
- Description
- Claims
- Application Information
AI Technical Summary
Problems solved by technology
Method used
Image
Examples
Embodiment 1
[0142] The positive and negative signs that define the current value of the motor. The positive sign indicates that the torque generated by the current makes the car obtain upward acceleration; the negative sign indicates that the torque generated by the current makes the car obtain downward acceleration;
[0143] Define the positive direction of displacement as the upward direction of the car;
[0144] The sampling period used by the control device is 5ms;
[0145] When residual friction force estimation is required (it can be triggered manually or automatically by the control device, not shown in the figure), the control device enters the residual friction force estimation mode; in this mode, the speed command generation unit issues a specific speed Command to direct the car to run to the same floor in the upward and downward directions; the residual friction estimation part reads the speed command, motor motion state feedback signal and brake action signal (not shown in the figure...
Embodiment 2
[0200] Compared with the embodiment 1, the method of estimating the residual friction is different in this embodiment; the other parts are the same;
[0201] When estimating the residual friction force, when the car is at no load, half load and full load, use the formula (4) described in Example 1 to calculate the residual friction currents corresponding to the three loads:
[0202] I rf_N ……No-load residual friction current
[0203] I rf_B ……Half-load residual friction current
[0204] I rf_F ……Full load residual friction current
[0205] When the system is working normally, assuming that the ratio of the load in the car to the full load value is p, if the car was going up last time, the residual friction current estimation method is:
[0206] I rf =(2I rf_F -4I rf_B +2I rf_N )p 2 +(-I rf_F +4I rf_B -3I rf_N )p+I rf_N Formula (20)
[0207] If the car was going down last time, the estimation method of residual friction current is:
[0208] I rf =-(2I rf_F -4I rf_B +2I rf_N )...
Embodiment 3
[0210] In this embodiment, the method for estimating the residual friction force is the same as that of Embodiment 1 or Embodiment 2; the method for estimating the maximum friction force is the same as that of Embodiment 1;
[0211] When the elevator system needs to be started, apply the pre-energized current I according to the formula (7) described in embodiment 1 pre ;
[0212] Then the control device drives the brake to release and applies a specific speed command V pre , And enable the speed command follower; where V pre The smaller the value, the stronger the effect of suppressing the startup vibration; but V pre Too small will cause too long waiting time when the system starts; therefore, the above factors should be considered comprehensively to select V pre Value; here will V pre Take 0.05m / s, and its direction is the current running direction of the car;
[0213] At this time, the current I applied to the motor is:
[0214] I=I wgh +I rf-l +I cont Formula (22)
[0215]...
PUM
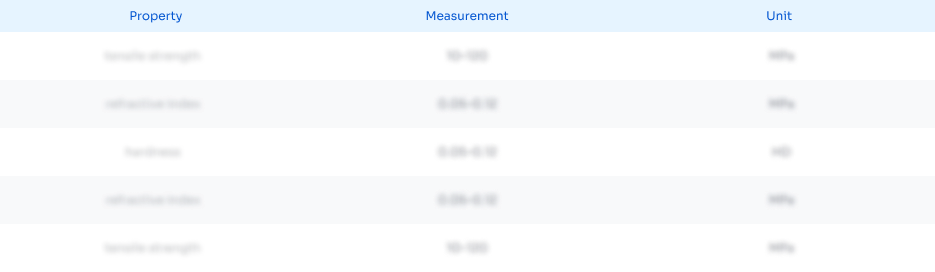
Abstract
Description
Claims
Application Information

- R&D
- Intellectual Property
- Life Sciences
- Materials
- Tech Scout
- Unparalleled Data Quality
- Higher Quality Content
- 60% Fewer Hallucinations
Browse by: Latest US Patents, China's latest patents, Technical Efficacy Thesaurus, Application Domain, Technology Topic, Popular Technical Reports.
© 2025 PatSnap. All rights reserved.Legal|Privacy policy|Modern Slavery Act Transparency Statement|Sitemap|About US| Contact US: help@patsnap.com