Changeable rigidity flexibility actuator
A flexible driver and variable stiffness technology, which is applied in the direction of manipulators, joints, manufacturing tools, etc., can solve the problems of small stiffness adjustment range, limited application effect, miniaturized joint design, complex structure, etc., and achieve fast adjustment and significant social and economic benefits and application prospects, the effect of simple structure
- Summary
- Abstract
- Description
- Claims
- Application Information
AI Technical Summary
Problems solved by technology
Method used
Image
Examples
Embodiment Construction
[0019] The invention provides a variable stiffness flexible driver. The present invention will be further described below in conjunction with the accompanying drawings and embodiments.
[0020] The variable stiffness flexible driver is composed of a power transmission mechanism and a stiffness adjustment mechanism.
[0021] powertrain such as figure 1 and figure 2 As shown, the main frame of the present invention is a frame 1, and a motor support 2 is installed on the frame 1; the main motor 3 is fixed on the motor support 2 through a flange, and is connected to the power input shaft 5 through the main motor coupling 4; The cross-section of the power input shaft 5 is square, on which a sliding sleeve 6 with an annular groove is slidably arranged; the power output shaft 9 is installed on the frame 1 through the bearing seat 8, and a bearing 10 is installed at the bottom of the power output shaft 9; The circular top end of the power input shaft 5 is connected to the bearing ...
PUM
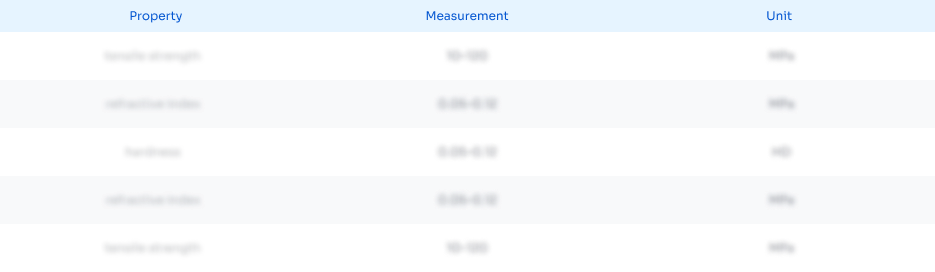
Abstract
Description
Claims
Application Information

- R&D
- Intellectual Property
- Life Sciences
- Materials
- Tech Scout
- Unparalleled Data Quality
- Higher Quality Content
- 60% Fewer Hallucinations
Browse by: Latest US Patents, China's latest patents, Technical Efficacy Thesaurus, Application Domain, Technology Topic, Popular Technical Reports.
© 2025 PatSnap. All rights reserved.Legal|Privacy policy|Modern Slavery Act Transparency Statement|Sitemap|About US| Contact US: help@patsnap.com