Multi-combined-station automatic core making center
An automatic manufacturing and station technology, applied in the direction of manufacturing tools, metal processing equipment, casting molding equipment, etc., can solve the problems affecting the quality of finished products, sand core damage, difficulties, etc., to reduce production costs, avoid damage to sand cores, reduce The effect of labor intensity
- Summary
- Abstract
- Description
- Claims
- Application Information
AI Technical Summary
Problems solved by technology
Method used
Image
Examples
Embodiment Construction
[0031]Below in conjunction with accompanying drawing and embodiment, further elaborate the present invention. In the following detailed description, certain exemplary embodiments of the invention are described by way of illustration only. Needless to say, those skilled in the art would realize that the described embodiments can be modified in various different ways, all without departing from the spirit and scope of the present invention. Accordingly, the drawings and description are illustrative in nature and not intended to limit the scope of the claims.
[0032] like figure 1 and figure 2 As shown, the multi-combination station automatic core-making center includes a sand-shooting rotary working device 1 and a core mold rotary working device 2 that cooperate with each other, and the sand-shooting rotary working device 1 and the core mold rotary working device 2 respectively correspond to A rotary drive mechanism 80 is provided;
[0033] like image 3 , Figure 4 and ...
PUM
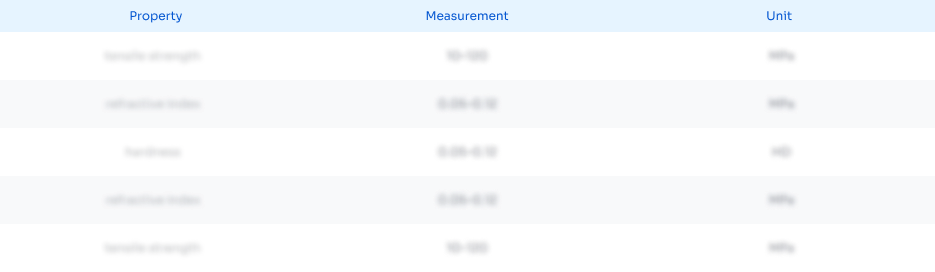
Abstract
Description
Claims
Application Information

- Generate Ideas
- Intellectual Property
- Life Sciences
- Materials
- Tech Scout
- Unparalleled Data Quality
- Higher Quality Content
- 60% Fewer Hallucinations
Browse by: Latest US Patents, China's latest patents, Technical Efficacy Thesaurus, Application Domain, Technology Topic, Popular Technical Reports.
© 2025 PatSnap. All rights reserved.Legal|Privacy policy|Modern Slavery Act Transparency Statement|Sitemap|About US| Contact US: help@patsnap.com