Gravitation separation tailing cassiterite flotation method
A technology for gravity separation of tailings and flotation, applied in flotation, chemical instruments and methods, magnetic separation, etc., can solve the problems of reducing recovery rate, affecting the utilization rate of shaking table, affecting the classification effect, etc.
- Summary
- Abstract
- Description
- Claims
- Application Information
AI Technical Summary
Problems solved by technology
Method used
Image
Examples
Embodiment 1
[0087] Embodiment 1 tin phase analysis
[0088] The phase analysis of tin in gravity separation tailings is shown in Table 1.
[0089] Table 1 Phase analysis of tin in gravity separation tailings
[0090] mineral name
[0091] The phase analysis shows that the tin grade of gravity separation tailings is 0.72%, among which the tin minerals are mainly cassiterite, the tin content in cassiterite occupies 79.17%, the tin content in phryotinite occupies 13.89%, and the colloidal tin ore The tin content in it accounts for 6.94%. Owing to the existence of zurtzite and colloidal tin, and the total amount accounts for 20.83%, it will have an adverse effect on the recovery rate of tin flotation.
Embodiment 2
[0092] The particle size analysis of embodiment 2 tin
[0093] After sampling and chemical analysis of the gravity separation tailings, the gravity separation tailings contain 0.33% lead, 0.15% zinc and 0.68% tin. The water analysis results of gravity separation tailings sieve are shown in Table 2.
[0094] It can be seen from Table 2 that the -74μm content of the gravity separation tailings is 48.97%, and the Sn metal is mainly distributed in the -74μm+38μm particle size and -38μm+10μm particle size, and the distribution rates are 28.39% and 33.92%, respectively. The distribution rate is 13.85%. According to the identification under the microscope, in the -74μm+10μm particle size, cassiterite mainly exists in the form of monomers, and a very small amount is associated organisms; in the -150μm+74μm particle size, the distribution rate accounts for 21.69%, but cassiterite exists in the form of associated organisms It accounts for half of the total, and a small amount is fine-...
Embodiment 3
[0097] Embodiment 3 Gravity separation tailings industrial application technical scheme
PUM
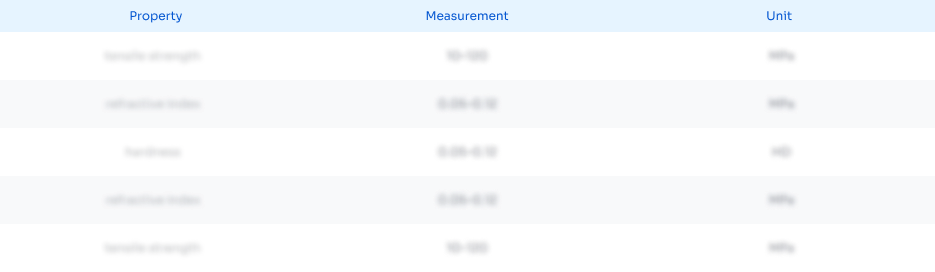
Abstract
Description
Claims
Application Information

- R&D Engineer
- R&D Manager
- IP Professional
- Industry Leading Data Capabilities
- Powerful AI technology
- Patent DNA Extraction
Browse by: Latest US Patents, China's latest patents, Technical Efficacy Thesaurus, Application Domain, Technology Topic, Popular Technical Reports.
© 2024 PatSnap. All rights reserved.Legal|Privacy policy|Modern Slavery Act Transparency Statement|Sitemap|About US| Contact US: help@patsnap.com