Assembled monolithic concrete large-span frame structure system and assembling method thereof
A technology of frame structure and assembly method, applied in the direction of truss structure, beam, building structure, etc.
- Summary
- Abstract
- Description
- Claims
- Application Information
AI Technical Summary
Problems solved by technology
Method used
Image
Examples
Embodiment 1
[0115] Such as Figure 4 As shown, a prefabricated frame column 4 is provided with at least two corbels on the upper part of the prefabricated frame column. Multiple corbels intersect or differ along the extension lines of the prefabricated frame column direction. When the prefabricated frame column 4 is provided with two corbels, it is a prefabricated frame corner column 4-1; when the prefabricated frame column 4 is provided with three corbels, it is a prefabricated frame side column 4-2; When the column 4 is provided with four corbels, it is the middle column 4-3 of the prefabricated frame.
[0116] The bottom or / and top of the prefabricated frame column 4 are provided with snap-in buckles 4-5, and the stay of the snap-in buckle 4-5 can ensure that the upper and lower prefabricated frame columns are connected horizontally when the sleeve grouting connection or slurry anchor connection is performed. The grouting material at the joint position is dense and full, and will not...
Embodiment 2
[0123] Such as Figure 8 Shown, a kind of prefabricated frame beam, its section is rectangle, L shape 5-2 or inverted T shape 5-1, the beam side of prefabricated frame beam is provided with vertical groove 5-3, and described vertical groove 5 -3 horizontally arranged. The two ends of the prefabricated frame beams are embedded with sleeves or reserved horizontal channels or embedded connectors 9 (such as Figure 17 shown) or embedded shield connector 11 (such as Figure 18 shown). The embedded sleeve or the reserved horizontal channel is used for connecting with the prefabricated frame column. The embedded connector 9 and the embedded shield connector 11 are used to connect with the embedded socket 8 and the embedded bolt sleeve 10 of the prefabricated frame column respectively (such as Figure 17 , 18 shown). On the contrary, prefabricated frame columns can be pre-embedded connectors or pre-embedded shield connectors; and pre-embedded socket slots or pre-embedded bolt sl...
Embodiment 3
[0126] Such as Figure 9 , 10 As shown, a prefabricated truss girder 6 is provided with a groove 6-1 at its end for matching with a corbel of a prefabricated frame column. The prefabricated truss girder 6 is a hollow beam. The section of the hollow form beam is box-shaped 6-3 and I-shaped 6-2. The side of the prefabricated truss beam is provided with shear teeth 6-5, and the shear teeth 6-5 can strengthen the connection between the prefabricated truss beam and the prefabricated slab, effectively transmit horizontal stress, and enhance the integrity of the structure. The prefabricated truss girder is a solid beam, such as a rectangular 6-4 section. The prefabricated truss beams are arch beams. The prefabricated truss girders are provided with reserved weldments or bolt connections for connecting with prefabricated frame columns. The exposed steel bars at the top of the prefabricated truss girder can be closed hoop-type or open-type short bars. The stressed steel bars of t...
PUM
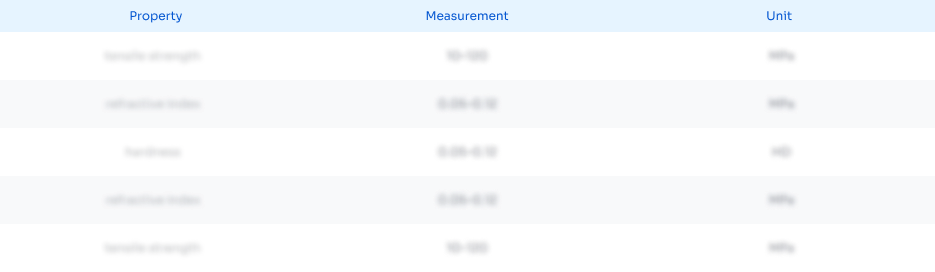
Abstract
Description
Claims
Application Information

- R&D Engineer
- R&D Manager
- IP Professional
- Industry Leading Data Capabilities
- Powerful AI technology
- Patent DNA Extraction
Browse by: Latest US Patents, China's latest patents, Technical Efficacy Thesaurus, Application Domain, Technology Topic, Popular Technical Reports.
© 2024 PatSnap. All rights reserved.Legal|Privacy policy|Modern Slavery Act Transparency Statement|Sitemap|About US| Contact US: help@patsnap.com