Extruding method for two-dimension function-variation continuous variable-cross-section profile
An extrusion method and continuous technology, applied in the field of two-dimensional function-variable continuous variable-section profile extrusion, can solve problems such as difficulty in ensuring forming accuracy, and achieve the effects of high production efficiency, accurate size control, and simple equipment
- Summary
- Abstract
- Description
- Claims
- Application Information
AI Technical Summary
Problems solved by technology
Method used
Image
Examples
Embodiment 1
[0025] 1. Machining 2024 aluminum alloy raw materials into prefabricated blank size;
[0026] 2. Keep the prefabricated blank in the temperature range of 450-470°C for 2 hours;
[0027] 3. Control the temperature of the extrusion cylinder and the molding die at 430-450°C; complete the adjustment of the motion control servo device, the load-bearing die and the forming die. That is to ensure that the maximum gap between the load-bearing mold a and the load-bearing mold b is smaller than the cavity size of the mold, and the minimum gap is greater than zero; ensure that the maximum gap between the forming mold c and the forming mold d is smaller than the mold cavity size, and the minimum gap is equal to the mold cavity size The minimum dimension in the direction of the cross section; to ensure that the forming mold lags behind the matching bearing mold for 1 second when it is fed inward, and ensures that the forming mold is ahead of the matching bearing mold for 1 second when it w...
Embodiment 2
[0032] 1. Machining 6061 aluminum alloy raw materials into prefabricated billet size;
[0033] 2. Heat the 6061 aluminum alloy prefabricated billet in the temperature range of 500-520°C for 1.5 hours;
[0034] 3. Control the temperature of the extrusion cylinder and the molding die at 490-500°C; complete the adjustment of the motion control servo device, the load-bearing mold and the forming mold. That is to ensure that the maximum gap between the load-bearing mold a and the load-bearing mold b is smaller than the cavity size of the mold, and the minimum gap is greater than zero; ensure that the maximum gap between the forming mold c and the forming mold d is smaller than the mold cavity size, and the minimum gap is equal to the mold cavity size The minimum size in the direction of the cross section; ensure that the forming die lags behind the matching load-bearing die by 0.5 seconds when it is fed inward, and ensures that the forming die is ahead of the matching load-bearing ...
Embodiment 3
[0039] 1. The AZ31 magnesium alloy raw material is machined into prefabricated billet size;
[0040] 2. Keep the AZ31 magnesium alloy prefabricated blank in the temperature range of 380-390°C for 1 hour;
[0041] 3. Control the temperature of the extrusion cylinder and the molding die within 370-480°C; complete the adjustment of the motion control servo device, the load-bearing mold and the forming mold. That is to ensure that the maximum gap between the load-bearing mold a and the load-bearing mold b is smaller than the cavity size of the mold, and the minimum gap is greater than zero; ensure that the maximum gap between the forming mold c and the forming mold d is smaller than the mold cavity size, and the minimum gap is equal to the mold cavity size The minimum size in the direction of the cross section; ensure that the forming die lags behind the matching load-bearing die by 0.75 seconds when it is fed inward, and ensures that the forming die is ahead of the matching load-...
PUM
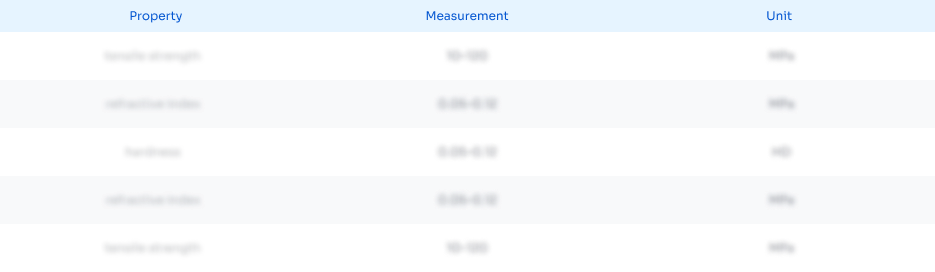
Abstract
Description
Claims
Application Information

- R&D
- Intellectual Property
- Life Sciences
- Materials
- Tech Scout
- Unparalleled Data Quality
- Higher Quality Content
- 60% Fewer Hallucinations
Browse by: Latest US Patents, China's latest patents, Technical Efficacy Thesaurus, Application Domain, Technology Topic, Popular Technical Reports.
© 2025 PatSnap. All rights reserved.Legal|Privacy policy|Modern Slavery Act Transparency Statement|Sitemap|About US| Contact US: help@patsnap.com