Regeneration method for catalyst containing precious metal and molecular sieve
A catalyst and noble metal technology, applied in the field of deactivated catalyst regeneration, can solve the problems of difficult separation of macromolecular by-products, molecular sieve structure damage, metal platinum aggregation, etc., to improve hydrogenation/dehydrogenation reaction activity, improve dispersion, good Dispersion effect
- Summary
- Abstract
- Description
- Claims
- Application Information
AI Technical Summary
Problems solved by technology
Method used
Image
Examples
Embodiment 1
[0032] Preparation of Catalyst E-1 of the Invention.
[0033] Add 1450ml of organic solvent (the volume ratio of ethanol and benzene is 2:1) into a 2000ml flask, and carry out deactivation of the catalyst (FD-1, Pt content 0.45 wt%, carbon content 7.24wt% the same below) after industrial operation. After processing, the catalyst number after 2 hours of distillation was Ca-1.
[0034] Take 120g of Ca-1 catalyst, add 14.4g of zinc nitrate (Zn content 5.0wt%) solution for impregnation, and prepare a Zn-containing sample with an atomic ratio of Zn to Pt of 4:1, and then at a heating rate of 3°C / min, Raise the temperature to 250°C for 10 hours, and then continue to raise the temperature to 410°C for 3 hours at a rate of 3°C / min. The obtained catalyst is numbered Ea-1.
[0035] Add 8.5wt% (as HNO 3 Add 100 g of the above-mentioned catalyst Ea-1 to 300 g of nitric acid aqueous solution, soak at room temperature for 10 hours, and then dry at 120° C. for 10 h to obtain catalyst E-1 o...
Embodiment 2
[0037] The preparation of catalyst E-2 of the present invention
[0038] Take 120g of Ca-1 catalyst, add 15g of zinc acetate (Zn content 10.0wt%) solution for impregnation to prepare a Zn-containing sample, wherein the atomic ratio of Zn to Pt is 5:1, and then heat up at a rate of 3°C / min , heated to 230° C. for 10 hours, and then continued to heat up to 420° C. for 3 hours at a rate of 3° C. / min. The obtained catalyst was numbered Eb-1.
[0039] Add 7.5wt% (as HNO 3 Add 100 g of the above-mentioned catalyst Eb-1 to 300 g of nitric acid aqueous solution, soak at room temperature for 5 hours and then dry at 110° C. for 8 hours to obtain catalyst E-2 of the present invention.
Embodiment 3
[0041] The preparation of catalyst E-3 of the present invention
[0042] Add 1450ml of organic solvent (the volume ratio of gasoline and kerosene is 1:1) into a 2000ml flask to treat the deactivated catalyst FD-1 after industrial operation, and the catalyst number after 2 hours of distillation is Cb-1.
[0043] Take 120g of Cb-1 catalyst, add 72g of zinc nitrate (Zn content 2.0wt%) solution for impregnation to prepare a Zn-containing sample, wherein the atomic ratio of Zn to Pt is 8:1, and then heat up at a rate of 3°C / min , heated to 280°C for 8 hours, and then continued to heat up to 350°C for 5 hours at a rate of 3°C / min. The obtained catalyst was numbered Ec-1.
[0044] Add 15% (as HNO 3 Add 100 g of the above-mentioned catalyst Ec-1 to 300 g of nitric acid aqueous solution, soak at room temperature for 10 hours, and then dry at 120° C. for 10 hours to obtain the catalyst E-3 of the present invention. Its physical and chemical properties are shown in Table 3, and the rea...
PUM
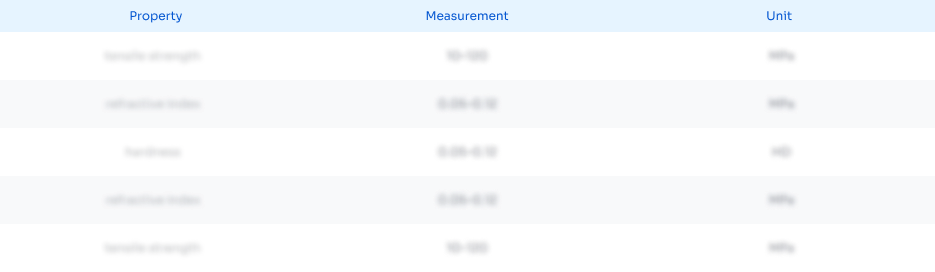
Abstract
Description
Claims
Application Information

- Generate Ideas
- Intellectual Property
- Life Sciences
- Materials
- Tech Scout
- Unparalleled Data Quality
- Higher Quality Content
- 60% Fewer Hallucinations
Browse by: Latest US Patents, China's latest patents, Technical Efficacy Thesaurus, Application Domain, Technology Topic, Popular Technical Reports.
© 2025 PatSnap. All rights reserved.Legal|Privacy policy|Modern Slavery Act Transparency Statement|Sitemap|About US| Contact US: help@patsnap.com