Processing technology and processing equipment of 3D printing wire
A 3D printing and processing technology, applied in the direction of additive processing, etc., can solve the problems of locked screw, difficult to process multi-color 3D wire, etc., to achieve the effect of reducing wear and improving quality observability
- Summary
- Abstract
- Description
- Claims
- Application Information
AI Technical Summary
Problems solved by technology
Method used
Image
Examples
Embodiment 1
[0040] The processing equipment for 3D printing wire includes a barrel and an extruder located directly below the barrel. A main feeding device 30A and a plurality of auxiliary material feeding devices are arranged at the mouth of the barrel. The main feeding device 30A The small screw and the screw of the extruder maintain a certain speed ratio and continue to run; there are five auxiliary material feeding devices above the extruder, which are the first auxiliary material feeding device C01, the second auxiliary material feeding device C02, The third auxiliary material feeding device C03, the fourth auxiliary material feeding device C04 and the fifth auxiliary material feeding device C05. Specifically, add additives to polylactic acid raw materials and mix them into barrel B, use 10 grams of toners in five colors of red, green, yellow, blue, and orange, and mix them with 800 grams of polylactic acid raw materials evenly, and the diluted The toner is respectively put into the ...
Embodiment 2
[0042] control image 3 : Mix the dried polylactic acid raw materials and additives into the barrel, use 10 grams of red, green and yellow toners, mix and dilute the toners with 800 grams of dried polylactic acid raw materials, and then put in auxiliary materials in turn In the barrel of the feeding device, adjust the frequency converters of the extruder and the main feeding device to 23 and 2.3HZ respectively, the machine rotates, and the diluted toner is added as red-yellow-green-yellow-red, which is defined as C1-C3-C2-C3-C1, each adjacent two starts to rotate and feed at intervals of 10 seconds, and the next one rotates to feed when the previous one stops, and the red-yellow-green three colors can be extruded from the single-screw extruder Block gradient 3D printing filament. Among them, C1 in the figure represents the auxiliary material feeding device with red toner added, and so on for C2 and C3.
PUM
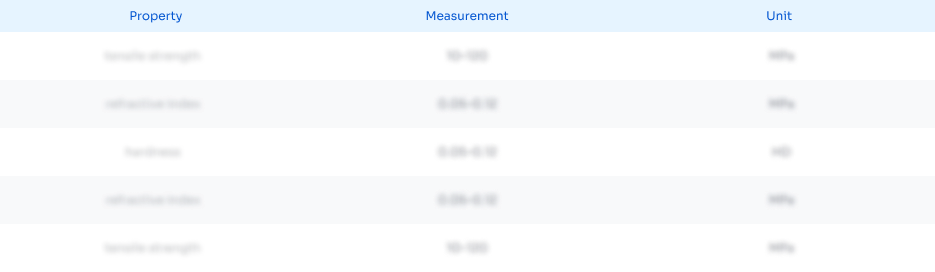
Abstract
Description
Claims
Application Information

- R&D Engineer
- R&D Manager
- IP Professional
- Industry Leading Data Capabilities
- Powerful AI technology
- Patent DNA Extraction
Browse by: Latest US Patents, China's latest patents, Technical Efficacy Thesaurus, Application Domain, Technology Topic, Popular Technical Reports.
© 2024 PatSnap. All rights reserved.Legal|Privacy policy|Modern Slavery Act Transparency Statement|Sitemap|About US| Contact US: help@patsnap.com