Magneto-rheological compliant controller for robot joints
A robot joint and magneto-rheological technology, applied in the field of robotics, can solve the problems of not being able to have rigidity and passive flexibility at the same time
- Summary
- Abstract
- Description
- Claims
- Application Information
AI Technical Summary
Problems solved by technology
Method used
Image
Examples
Embodiment Construction
[0012] The present invention will be further described below in conjunction with the accompanying drawings.
[0013] refer to Figure 1 ~ Figure 3 , a magneto-rheological compliance controller for robot joints, a sealed cavity 3, a first gear 4, a second gear 5 and an electromagnetic coil 6, the sealed cavity 3 is filled with magnetorheological fluid 7, the sealed cavity The body 1 is provided with a first gear 4 and a second gear 5, the first gear 4 and the second gear 5 mesh, the first gear shaft 8 of the first gear 4, the second gear shaft 9 of the second gear 5 They all protrude from the sealed cavity respectively, and the electromagnetic coil 6 used to change the magnetic field strength in the sealed cavity is installed on the side of the sealed cavity 3, and the first gear shaft 8 or the second gear shaft 9 is used to drive The driving mechanism that the first gear or the second gear rotates is connected.
[0014] Further, the first gear shaft 8 is fixedly installed on...
PUM
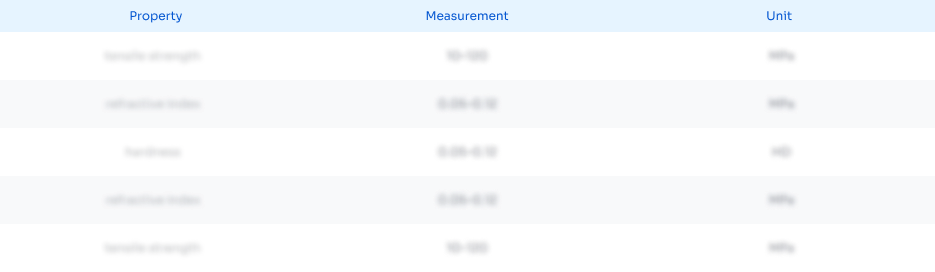
Abstract
Description
Claims
Application Information

- R&D
- Intellectual Property
- Life Sciences
- Materials
- Tech Scout
- Unparalleled Data Quality
- Higher Quality Content
- 60% Fewer Hallucinations
Browse by: Latest US Patents, China's latest patents, Technical Efficacy Thesaurus, Application Domain, Technology Topic, Popular Technical Reports.
© 2025 PatSnap. All rights reserved.Legal|Privacy policy|Modern Slavery Act Transparency Statement|Sitemap|About US| Contact US: help@patsnap.com