Double-side polishing method of 12-inch silicon wafer
A double-sided polishing, silicon wafer technology, applied in the polishing field, can solve problems such as uneven wear of polishing pads, and achieve the effects of improving the amount of wear, slowing down the glazing speed, and reducing the number of dressing times.
- Summary
- Abstract
- Description
- Claims
- Application Information
AI Technical Summary
Problems solved by technology
Method used
Image
Examples
Embodiment 1
[0024] Choose 400 pieces of 12-inch P(100) silicon wafers grown by the Czochralski method, divided into four groups A, B, C, and D, with 100 pieces in each group. After single-side grinding, the thickness is about 800 μm, all in SPEEDFAM20B Polishing was carried out on a double-sided polishing machine, 5 silicon wafers were polished per plate, the polishing pad was SUBA800, and the polishing removal amount was 25 μm (polishing time was about 50 minutes).
[0025] For group A, the conventional method is used for polishing, that is, the relative movement direction of the cruiser plate and the polishing pad remains unchanged, and the polishing is carried out continuously without brushing or repairing between the discs; for group B, the conventional method is used for polishing. After polishing a silicon wafer, use a brush to scrub the polishing pad without repairing the disk; for group C, use the conventional method for polishing. After polishing a silicon wafer, use a brush to sc...
Embodiment 2
[0029] The two polishing cloths E and F were both polished on both sides normally using the scheme of Group D in Example 1. When the polishing machine is stopped, do not spray water on the surface of the polishing cloth E, and let it dry naturally; for the polishing cloth F, use water circulation to keep the surface of the polishing cloth wet. Ultimately, Cloth E had a service life of 60 hours, and Cloth F had a service life of 80 hours. It can be seen that when the polishing machine is stopped, pure water circulates through the polishing liquid pipeline to keep the surface of the polishing cloth moist and prolong the service life of the polishing cloth.
PUM
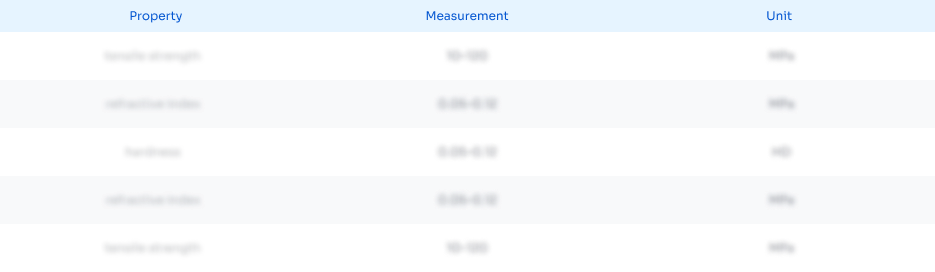
Abstract
Description
Claims
Application Information

- Generate Ideas
- Intellectual Property
- Life Sciences
- Materials
- Tech Scout
- Unparalleled Data Quality
- Higher Quality Content
- 60% Fewer Hallucinations
Browse by: Latest US Patents, China's latest patents, Technical Efficacy Thesaurus, Application Domain, Technology Topic, Popular Technical Reports.
© 2025 PatSnap. All rights reserved.Legal|Privacy policy|Modern Slavery Act Transparency Statement|Sitemap|About US| Contact US: help@patsnap.com