Inverted jet stream and orifice designing method capable of reducing drag and preventing heat for hypersonic flight vehicle
A technology of hypersonic speed and design method, applied in the direction of affecting the air flow flowing through the surface of the aircraft, aircraft parts, aircraft control, etc., can solve the problems that can not significantly improve the characteristics of drag reduction and heat protection, and achieve optimal drag reduction and heat protection characteristics, performance-enhancing effects
- Summary
- Abstract
- Description
- Claims
- Application Information
AI Technical Summary
Problems solved by technology
Method used
Image
Examples
Embodiment Construction
[0023] In the supersonic incoming flow, it is very complicated to adopt the flow mode of reverse jet flow, such as figure 1 As shown, it includes secondary compression shock wave 1, recirculation zone 2, jet layer 3, Mach disk 4, separation shock wave 5 and contact surface 6, of which 7 is the nozzle hole. m ∞ is the incoming Mach number, P 0∞ is the total pressure of incoming flow, M j is the jet Mach number, P 0j is the total jet pressure. The Mach disk 4 in the flow field balances the pressure of the jet flow and the pressure of the incoming flow after the bow shock wave, and forms a contact surface 6 at the outer end of the Mach disk 4. The reverse jet flow forms a recirculation area under the action of the incoming flow, and then attaches to the surface. The free flow forms a bow shock wave under the reverse action of the jet flow, and forms a secondary compression shock wave at the outer edge of the recirculation zone boundary. Due to the existence of the recircula...
PUM
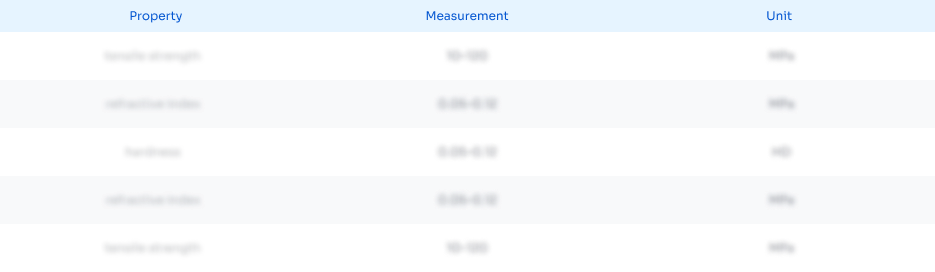
Abstract
Description
Claims
Application Information

- R&D Engineer
- R&D Manager
- IP Professional
- Industry Leading Data Capabilities
- Powerful AI technology
- Patent DNA Extraction
Browse by: Latest US Patents, China's latest patents, Technical Efficacy Thesaurus, Application Domain, Technology Topic.
© 2024 PatSnap. All rights reserved.Legal|Privacy policy|Modern Slavery Act Transparency Statement|Sitemap