Continuous casting and rolling device and process for composite plate
A technology of continuous casting, rolling, and cladding plates, applied in metal rolling and other directions, can solve the problems of incapable of continuous cladding production of clad plates, large energy consumption, affecting production efficiency, etc., achieving continuous casting and rolling technology and saving production costs. , the effect of improving production efficiency
- Summary
- Abstract
- Description
- Claims
- Application Information
AI Technical Summary
Problems solved by technology
Method used
Image
Examples
Embodiment Construction
[0032] The present invention will be further described below in conjunction with accompanying drawing:
[0033] Such as figure 1 As shown in the overall structure diagram of the equipment of the present invention, the present invention mainly includes a continuous casting machine main body 1, a first ladle turret 2 and a second ladle turret 3, a tundish installation platform 4, a first tundish 5, a second tundish 6. First crystallizer 9, second crystallizer 10, composite zone 11, squeeze roll 12, press roll 13, secondary cooling zone 14, tension leveler 15, flame cutting device 16, descaler 17 and continuous rolling Crew 18,
[0034]The first ladle turret is installed on the top of the main body of the continuous casting machine, a tundish installation platform is installed on the main body of the continuous casting machine below the first ladle turret, the first tundish is installed on the tundish installation platform, and the first tundish is installed on the lower part of...
PUM
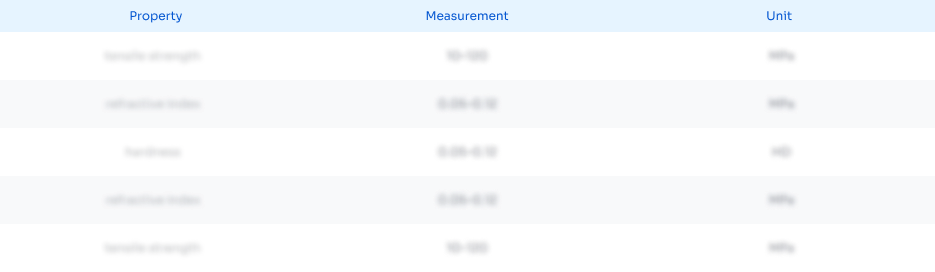
Abstract
Description
Claims
Application Information

- Generate Ideas
- Intellectual Property
- Life Sciences
- Materials
- Tech Scout
- Unparalleled Data Quality
- Higher Quality Content
- 60% Fewer Hallucinations
Browse by: Latest US Patents, China's latest patents, Technical Efficacy Thesaurus, Application Domain, Technology Topic, Popular Technical Reports.
© 2025 PatSnap. All rights reserved.Legal|Privacy policy|Modern Slavery Act Transparency Statement|Sitemap|About US| Contact US: help@patsnap.com