A Thermally Coupled Jet Parallel Flow Tower with Heat Exchange Trays
A heat exchange tray and thermal coupling technology, applied in fractionation and other directions, can solve the problems of small internal thermal coupling heat transfer area, difficult popularization and application, high cost, easy installation, maintenance and production operation, large economic benefits and application prospects , the effect of saving operating costs
- Summary
- Abstract
- Description
- Claims
- Application Information
AI Technical Summary
Problems solved by technology
Method used
Image
Examples
Embodiment Construction
[0025] Below in conjunction with embodiment and accompanying drawing, the present invention is described in further detail:
[0026] A thermally coupled jet parallel flow tower, comprising a cylindrical tower body 1; the tower body 1 includes a cylindrical inner tower 8 and an annular outer tower 9, the inner tower 8 is set in the outer tower 9; the inner tower 8 and the outer tower 9 The space is separated into a rectification section and a stripping section by the outer wall of the inner tower 8. When the inner tower 8 is the rectification section, the outer tower 9 is the stripping section; when the inner tower 8 is the stripping section, the outer tower 9 is the rectification section. A reboiler 14 for providing heat to the tower body is arranged at the bottom of the tower, and the reboiler 14 is connected with the bottom of the stripping section; a condenser 15 and a reflux pump 17 are arranged at the top of the rectifying section.
[0027] The structure of the outer tow...
PUM
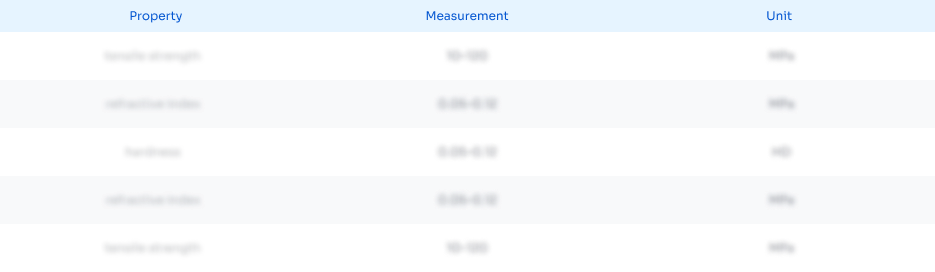
Abstract
Description
Claims
Application Information

- R&D
- Intellectual Property
- Life Sciences
- Materials
- Tech Scout
- Unparalleled Data Quality
- Higher Quality Content
- 60% Fewer Hallucinations
Browse by: Latest US Patents, China's latest patents, Technical Efficacy Thesaurus, Application Domain, Technology Topic, Popular Technical Reports.
© 2025 PatSnap. All rights reserved.Legal|Privacy policy|Modern Slavery Act Transparency Statement|Sitemap|About US| Contact US: help@patsnap.com