A Method for Preventing Dislocation of Local Mixed Plates
A mixed pressure and partial technology, applied in the direction of stacking printed circuit boards, printed circuits, electrical components, etc., can solve the problems of poor PCB board production quality, easy misalignment of daughter boards and motherboards, etc., and achieve low scrap rate and high production quality. high effect
- Summary
- Abstract
- Description
- Claims
- Application Information
AI Technical Summary
Problems solved by technology
Method used
Image
Examples
Embodiment 1
[0033] Such as Figure 1-2 As shown, a method for preventing partial mixed-press board misalignment described in Embodiment 1 includes a sub-board pretreatment step, a motherboard pre-treatment step, and a daughter-board motherboard mixing step;
[0034] After the sub-board pretreatment step, the following steps are carried out: forming several grooves 3 and / or bumps 4 on at least one edge of the sub-board 1;
[0035] After the mother board pretreatment step, the following steps are also carried out: on the corresponding edge of the mother board 2 suitable for the cavity in which the sub-board 1 is embedded, the protrusions 4 and the protrusions 4 and / or Groove 3;
[0036] The following steps are carried out before the mixed pressure step of the sub-board motherboard: the sub-board and the motherboard are inserted and matched with each other through the groove 3 and the protrusion 4 so that the sub-board 1 and the Embedded positioning is performed between the motherboards 2...
Embodiment 2
[0042] The difference between this embodiment and embodiment 1 is that in this embodiment 2, for the convenience of processing, only three grooves 3 are formed on two of the opposite edges of the sub-board 1, preferably two The grooves 3 on the edge are arranged in a staggered manner; three corresponding protrusions 4 are formed on two corresponding edges of the motherboard 2 .
Embodiment 3
[0044] The difference between this embodiment and Embodiments 1 and 2 is that, in this embodiment 3, grooves 3 and bumps 4 can be provided on the edge of the sub-board 1 at the same time, as Figure 5 As shown; the corresponding edge of the motherboard 2 can be provided with a mating projection 4 and a groove 3 at the same time, as Figure 6As shown; in this embodiment, only the case where the groove 3 and the protruding block 4 are provided at the two opposite edges of the sub-board at the same time, of course, it can also be set in this way on the three or four edges of the sub-board.
[0045] The shape of the groove 3 and the bump 4 in the above three embodiments can be in various shapes, such as a rectangular block, a pointed block or an arc block, and in the above three embodiments, In order to facilitate processing and smooth insertion at the insertion joint, it is preferable to set the groove 3 and the protrusion 4 as circular arc blocks.
PUM
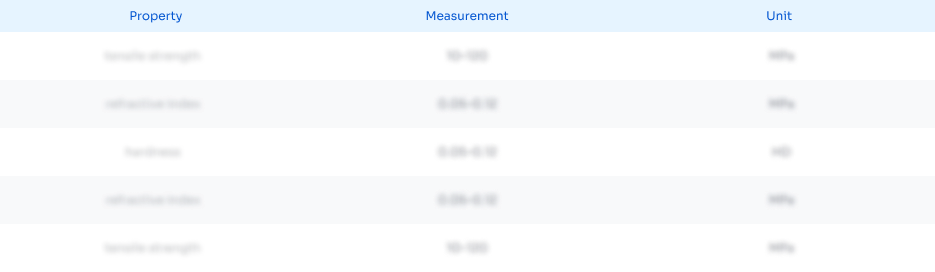
Abstract
Description
Claims
Application Information

- Generate Ideas
- Intellectual Property
- Life Sciences
- Materials
- Tech Scout
- Unparalleled Data Quality
- Higher Quality Content
- 60% Fewer Hallucinations
Browse by: Latest US Patents, China's latest patents, Technical Efficacy Thesaurus, Application Domain, Technology Topic, Popular Technical Reports.
© 2025 PatSnap. All rights reserved.Legal|Privacy policy|Modern Slavery Act Transparency Statement|Sitemap|About US| Contact US: help@patsnap.com