A method for optimizing operation of solvent dehydration system in aromatic acid production process
A technology for system optimization and production process, applied in chemical instruments and methods, separation/purification of carboxylic acid compounds, preparation of organic compounds, etc., can solve problems such as large reflux ratio and high acid consumption, and achieve increased reflux ratio and improved Purity, the effect of increasing energy consumption
- Summary
- Abstract
- Description
- Claims
- Application Information
AI Technical Summary
Problems solved by technology
Method used
Image
Examples
Embodiment 1
[0031] Terephthalic acid is produced by catalytic oxidation of p-xylene (PX) under a catalyst at a certain temperature and pressure. During the production process, the acetic acid aqueous solution cooled by the steam at the top of the oxidation reactor enters the upper part of the solvent dehydration tower T1.
[0032] Such as figure 1 As shown, the theoretical plate number of the solvent dehydration tower T1 is 60, the theoretical plate number of the entrainer refining tower T2 is 30, and the theoretical plate number of the methyl acetate recovery tower T3 is 30. The flow rate of the aqueous acetic acid solution entering the solvent dehydration tower is 1000kg / hr, which contains 70wt.% of acetic acid, 29.5wt.% of water, and 0.5wt.% of the quality of methyl acetate. Feed, after the overhead steam 2 is condensed, the condensate 3 enters the phase separator V1, and the concentrated acetic acid 4 extracted from the bottom of the solvent dehydration tower T1 and returned to the ox...
Embodiment 2
[0034] Keep other conditions constant in Example 1, the PX reflux flow rate is 740kg / hr, the reflux flow rate and the total amount ratio of entering the solvent dehydration tower T1 water are 2.5, and the concentrated acetic acid water content of the solvent dehydration tower T1 tower kettle returning to the oxidation unit is 3.5wt.%. , containing PX0.3wt.%, the content of acetic acid in the water phase of the methyl acetate recovery tower T3 is 0.02%, the reflux of the upper water phase of the solvent dehydration tower T1 is 60kg / hr, and the output of the water phase of the methyl acetate recovery tower T3 is It is 230kg / hr, and the reflux rate accounts for 20.1% of the total amount of water phase in the T3 tower kettle of the methyl acetate recovery tower. The extracted methyl acetate content is 98.0%.
Embodiment 3
[0036] Keep other conditions constant in Example 1, the PX reflux flow rate is 590kg / hr, the oil phase reflux flow rate and the total amount ratio of water entering the solvent dehydration tower T1 are 2, and the concentrated acetic acid in the solvent dehydration tower T1 tower kettle returns to the oxidation unit with a water content of 4.0wt .%, containing PX0.2wt.%, the content of acetic acid in the water phase of the tower kettle T3 of the methyl acetate recovery tower is 0.015%, the return flow rate of the water phase in the upper part of the solvent dehydration tower T1 is 75kg / hr, and the water phase of the methyl acetate recovery tower T3 The output is 215kg / hr, and the reflux rate accounts for 25.9% of the total amount of water phase in the tower tank of the methyl acetate recovery tower T3. The content of methyl acetate extracted from the top of the entrainer refining tower T2 is 98.1%. The content of methyl acetate produced at the top of the tower is 98.2%.
PUM
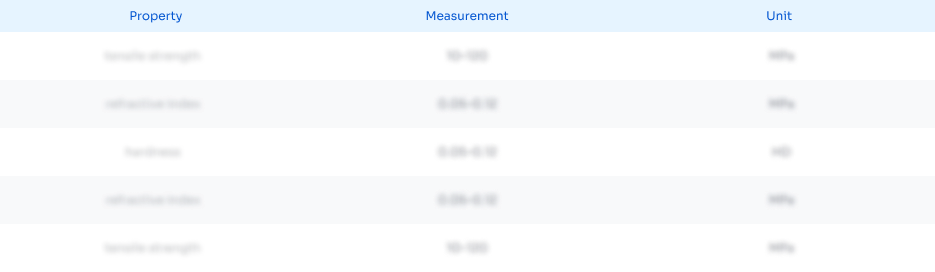
Abstract
Description
Claims
Application Information

- Generate Ideas
- Intellectual Property
- Life Sciences
- Materials
- Tech Scout
- Unparalleled Data Quality
- Higher Quality Content
- 60% Fewer Hallucinations
Browse by: Latest US Patents, China's latest patents, Technical Efficacy Thesaurus, Application Domain, Technology Topic, Popular Technical Reports.
© 2025 PatSnap. All rights reserved.Legal|Privacy policy|Modern Slavery Act Transparency Statement|Sitemap|About US| Contact US: help@patsnap.com