Double-shaft split type differential silicon micromachined resonant accelerometer
An accelerometer and resonant technology, which is applied in the field of dual-axis split differential silicon micro-resonant acceleration inertial sensors, can solve the problems of serious cross-coupling of differential resonators, achieve the effects of improving sensitivity, improving quality factor, and eliminating coupling effects
- Summary
- Abstract
- Description
- Claims
- Application Information
AI Technical Summary
Problems solved by technology
Method used
Image
Examples
Embodiment Construction
[0030] The present invention will be further described below in conjunction with the accompanying drawings.
[0031] A dual-axis split-type differential silicon microresonant accelerometer, such as figure 1 As shown, including the upper silicon micromechanical structure and the lower glass base, the upper silicon micromechanical structure is bonded on the lower glass base; the lower glass base is sputtered with signal leads, and the upper silicon micromechanical structure includes four The upper silicon micromechanical substructures are the first, second, third, and fourth upper silicon micromechanical substructures, and the first, second, third, and fourth upper silicon micromechanical substructures are arranged counterclockwise. On the lower glass base; among them, the differential structure formed by the first and fourth upper silicon micromechanical substructures constitutes the first group of acceleration measurement modules, and the differential structure formed by the s...
PUM
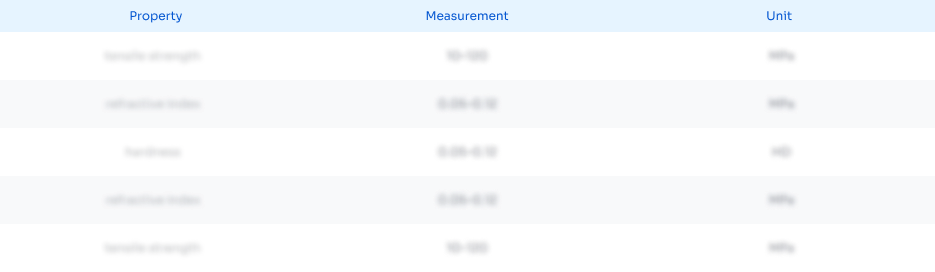
Abstract
Description
Claims
Application Information

- Generate Ideas
- Intellectual Property
- Life Sciences
- Materials
- Tech Scout
- Unparalleled Data Quality
- Higher Quality Content
- 60% Fewer Hallucinations
Browse by: Latest US Patents, China's latest patents, Technical Efficacy Thesaurus, Application Domain, Technology Topic, Popular Technical Reports.
© 2025 PatSnap. All rights reserved.Legal|Privacy policy|Modern Slavery Act Transparency Statement|Sitemap|About US| Contact US: help@patsnap.com