Cold-forging technology for safety belt transmission shaft and die structure of molded transmission patterned tooth
A technology for transmission shafts and safety belts, which is applied in the manufacture of tools, engine components, metal processing equipment, etc., can solve the problems of many processing procedures, waste of materials, and low processing efficiency, so as to reduce processing procedures, reduce production costs, and improve production efficiency effect
- Summary
- Abstract
- Description
- Claims
- Application Information
AI Technical Summary
Problems solved by technology
Method used
Image
Examples
Embodiment Construction
[0029] The present invention will be described in detail below in conjunction with the accompanying drawings.
[0030] Such as figure 1 Shown is a cold heading process for a seat belt transmission shaft, the process steps are:
[0031] S1, cutting wire;
[0032] S2, shaping the wire rod;
[0033] S3, strong beam rod;
[0034] S4, upsetting steps;
[0035] S5, strong rib teeth and punching;
[0036] S6, Shaping tendon teeth and beam small steps;
[0037] S7. Forming transmission flower teeth and rib teeth.
[0038] The wire is work hardened.
[0039] Such as Figure 7 A mold structure for forming transmission teeth in step S7 is shown, including a main mold unit and a die unit, the main mold unit includes a main mold sleeve 15, and a main mold back pad is provided at the bottom of the main mold sleeve 15 plate 22, the die unit includes a die set 8, a molding die 14 is arranged on the die set 8, and the upper part 16 of the main die, the middle part 17 of the main die a...
PUM
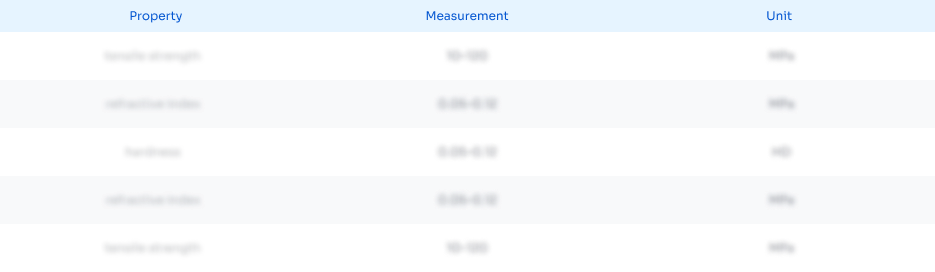
Abstract
Description
Claims
Application Information

- R&D
- Intellectual Property
- Life Sciences
- Materials
- Tech Scout
- Unparalleled Data Quality
- Higher Quality Content
- 60% Fewer Hallucinations
Browse by: Latest US Patents, China's latest patents, Technical Efficacy Thesaurus, Application Domain, Technology Topic, Popular Technical Reports.
© 2025 PatSnap. All rights reserved.Legal|Privacy policy|Modern Slavery Act Transparency Statement|Sitemap|About US| Contact US: help@patsnap.com