Method for making artificial rock core
A manufacturing method, technology of artificial rock core, applied in the field of petroleum exploration
- Summary
- Abstract
- Description
- Claims
- Application Information
AI Technical Summary
Problems solved by technology
Method used
Image
Examples
Embodiment 1
[0021] The river sand with the same particle size distribution as the natural core is selected as the skeleton particles. Mix river sand, epoxy resin and formation water according to the ratio in Table 1, and stir evenly. Clean the inside of the mold, and fill each mold with the prepared mixture of river sand and epoxy resin; place the mold filled with sand under the hydraulic press, and after the mold position is adjusted, use the hydraulic press to press the mold at 4MPa for 5 minutes. After the pressure is stable, release the pressure; put the pressed mold into the oven, bake at 100°C for 2 hours, then raise the temperature to 190°C and bake for 1 hour, then turn off the oven, let it cool naturally to room temperature from Remove the core from the mold. The cementation degree of the rock is expressed by the cementation index, and the greater the cementation index, the higher the cementation degree. The porosity, permeability and cementation index of the core are shown in ...
Embodiment 2
[0025] The river sand with the same particle size distribution as the natural core is selected as the skeleton particles. Mix river sand, epoxy resin and formation water according to the ratio in Table 2, and stir evenly. Clean the inside of the mold, and fill each mold with the prepared mixture of river sand and epoxy resin; place the mold filled with sand under the hydraulic press, and after the mold position is adjusted, use the hydraulic press to press the mold at 7MPa for 4 minutes. Release the pressure after the pressure is stable; put the pressed mold into the oven, bake at 110°C for 1.5 hours, then raise the temperature to 180°C and bake for 1.5 hours, then turn off the oven, let it cool naturally to room temperature from Remove the core from the mold. The cementation degree of the rock is expressed by the cementation index, and the greater the cementation index, the higher the cementation degree. The porosity, permeability and cementation index of the core are shown...
Embodiment 3
[0029] The river sand with the same particle size distribution as the natural core is selected as the skeleton particles. Mix the river sand, epoxy resin and formation water according to the ratio in Table 3, and stir evenly. Clean the inside of the mold, and fill each mold with the prepared mixture of river sand and epoxy resin; place the sand-filled mold under the hydraulic press, and after the mold position is adjusted, use the hydraulic press to press the mold at 10MPa for 4 minutes. Release the pressure after the pressure is stable; put the pressed mold into the oven, bake at 105°C for 1.8 hours, then raise the temperature to 185°C and bake for 1.2 hours, then turn off the oven, let it cool down to room temperature naturally Remove the core from the mold. The cementation degree of the rock is expressed by the cementation index, and the greater the cementation index, the higher the cementation degree. The porosity, permeability and cementation index of the core are shown...
PUM
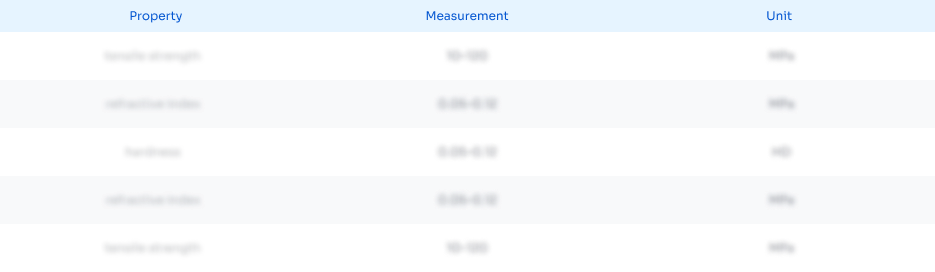
Abstract
Description
Claims
Application Information

- R&D Engineer
- R&D Manager
- IP Professional
- Industry Leading Data Capabilities
- Powerful AI technology
- Patent DNA Extraction
Browse by: Latest US Patents, China's latest patents, Technical Efficacy Thesaurus, Application Domain, Technology Topic, Popular Technical Reports.
© 2024 PatSnap. All rights reserved.Legal|Privacy policy|Modern Slavery Act Transparency Statement|Sitemap|About US| Contact US: help@patsnap.com