Synchronous oil supply and hold-down device for detecting high-pressure common-rail oil sprayer online and application method thereof
A common rail fuel injector and high pressure common rail technology, which is applied in the testing of measuring devices, fuel injection devices, and machine/structural components, etc., can solve the problem of low stability and reliability, oil leakage on the sealing surface, and affecting the sealing effect. and other problems, to achieve the effect of improving reliability and authenticity, improving high-pressure sealing performance, and improving detection efficiency
- Summary
- Abstract
- Description
- Claims
- Application Information
AI Technical Summary
Problems solved by technology
Method used
Image
Examples
specific Embodiment approach
[0024] A high-pressure common rail injector online detection synchronous oil supply and pressing device, such as figure 2 and image 3 As shown, it includes high-pressure oil injection joint 1, fastening nut sleeve 2, piston sleeve 3, pressure relief end cover 4, oil injection piston 5, fixed seat sleeve 6, cylinder 7, connecting plate 8, common rail injector to be inspected 9 and the injector installation sleeve 10, the high-pressure oil injection joint 1 is hermetically installed on the oil inlet end of the piston sleeve 3 through the fastening nut sleeve 2, and the oil injection piston 5 is provided with a stepped structure of an oil delivery hole 51 at the center, which consists of the first A guide section 52, a second guide section 53 and a butt joint 54 are composed. The first guide section 52 is set in the inner hole of the piston sleeve 3, the pressure relief end cap 4 is set on the second guide section 53, and the pressure relief end cover 4 Fixed on the piston sle...
PUM
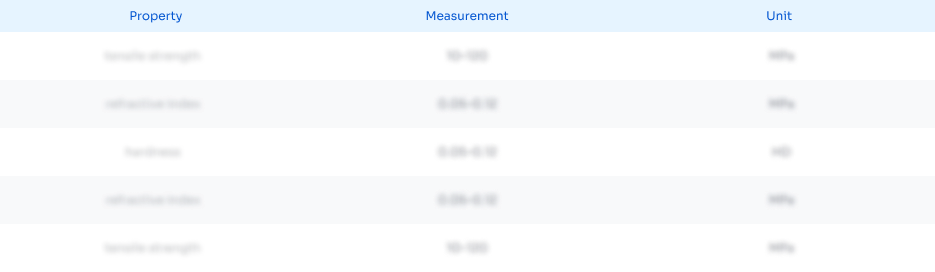
Abstract
Description
Claims
Application Information

- R&D Engineer
- R&D Manager
- IP Professional
- Industry Leading Data Capabilities
- Powerful AI technology
- Patent DNA Extraction
Browse by: Latest US Patents, China's latest patents, Technical Efficacy Thesaurus, Application Domain, Technology Topic, Popular Technical Reports.
© 2024 PatSnap. All rights reserved.Legal|Privacy policy|Modern Slavery Act Transparency Statement|Sitemap|About US| Contact US: help@patsnap.com