Method for manufacturing liquid inkjet head, liquid inkjet head, and printing apparatus
A technology of a liquid inkjet head and a manufacturing method, which is applied to the manufacture of liquid inkjet heads, the fields of liquid inkjet heads and printing equipment, can solve problems such as poor injection accuracy, and achieve the effect of improving printing speed
- Summary
- Abstract
- Description
- Claims
- Application Information
AI Technical Summary
Problems solved by technology
Method used
Image
Examples
Embodiment 1
[0045] figure 1 This is a flowchart of a method for manufacturing a liquid inkjet head provided in the first embodiment of the present invention. Such as figure 1 As shown, the manufacturing method of the liquid inkjet head may include:
[0046] Step 10. Form a pressure generating part on the substrate.
[0047] Step 20: forming a pressure chamber and a common chamber on the first surface of the substrate.
[0048] Step 30: Coating the first resin glue on the surface of the pressure chamber and the common chamber away from the substrate to form a spray hole glue layer.
[0049] Step 40: Perform grayscale exposure treatment on the orifice glue layer to form a cone-shaped orifice on the orifice glue layer at a position opposite to the pressure chamber. Along the direction away from the pressure chamber, the cross-sectional area of the orifice slowing shrieking.
[0050] The aforementioned substrate may be a silicon substrate or a glass substrate, and a silicon substrate is used in thi...
Embodiment 2
[0097] This embodiment provides another method for forming a pressure generating part on the basis of the above embodiment, which may specifically include:
[0098] The vibration plate 4 is deposited and formed on the first surface of the substrate 1.
[0099] Specifically, it can be formed by a low pressure chemical vapor deposition method or a plasma enhanced chemical vapor deposition method, and the material of the vibration plate 4 can be SiO 2 , Si 3 N 4 Or SiO 2 -Si 3 N 4 Of stacks. This step can refer to Picture 10 , Picture 10 It is a schematic structural diagram of forming a vibrating plate on the surface of the substrate in the method for manufacturing a liquid inkjet head according to the second embodiment of the present invention.
[0100] A piezoelectric element 3 is formed on the surface of the vibration plate 4 away from the substrate 1.
[0101] Specifically, a sputtering method may be used to form the lower electrode layer, a sol-gel method to form a piezoelectric l...
Embodiment 3
[0104] This embodiment provides yet another method for forming a pressure generating component on the basis of the foregoing embodiment, which specifically includes:
[0105] A thin film resistance layer 19 is deposited and formed on the first surface of the substrate 1.
[0106] Specifically, a thin film resistive layer 19 can be deposited on the substrate 1, and the material of the thin film resistive layer 19 can be one of tantalum aluminum alloy, nickel-cadmium alloy, tungsten silicon nitride, and titanium nitride. Can refer to Figure 13 , Figure 13 This is a schematic diagram of the structure of forming a thin film resistance layer on a substrate in the method for manufacturing a liquid inkjet head provided in the third embodiment of the present invention.
[0107] For the formation method of other components in the liquid inkjet head, reference may be made to the technical solutions provided in the above-mentioned embodiments, which will not be repeated here. The structure o...
PUM
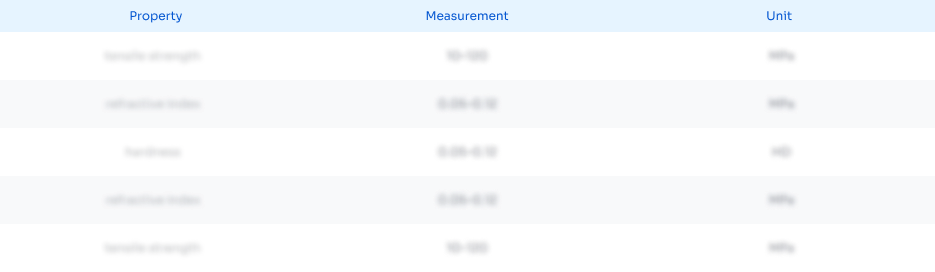
Abstract
Description
Claims
Application Information

- R&D
- Intellectual Property
- Life Sciences
- Materials
- Tech Scout
- Unparalleled Data Quality
- Higher Quality Content
- 60% Fewer Hallucinations
Browse by: Latest US Patents, China's latest patents, Technical Efficacy Thesaurus, Application Domain, Technology Topic, Popular Technical Reports.
© 2025 PatSnap. All rights reserved.Legal|Privacy policy|Modern Slavery Act Transparency Statement|Sitemap|About US| Contact US: help@patsnap.com