A large-space multi-degree-of-freedom controllable mechanism welding robot
A welding robot and degree-of-freedom technology, used in welding equipment, auxiliary welding equipment, program-controlled manipulators, etc., can solve the problems of limited length of connecting rod, small spatial positioning range, low manufacturing cost, etc., and can increase the expansion and contraction space. Effect
- Summary
- Abstract
- Description
- Claims
- Application Information
AI Technical Summary
Problems solved by technology
Method used
Image
Examples
Embodiment Construction
[0020] The technical solutions of the present invention will be clearly and completely described below in conjunction with the accompanying drawings and embodiments. Apparently, the embodiments are only a part of the embodiments of the present invention, not all of them. Based on the embodiments of the present invention, all other embodiments obtained by those skilled in the art without creative efforts fall within the protection scope of the present invention.
[0021] control figure 1 and figure 2 , a large-space multi-degree-of-freedom controllable mechanism welding robot, including a motor, a rotating base, a base moving mechanism, a vertical moving mechanism, a horizontal moving mechanism and a welding torch.
[0022] Described motor is controllable motor, is made up of the first controllable motor 4, the second controllable motor 15 and the 3rd controllable motor 22, the first controllable motor 4 is fixed on the base moving guide rail 3, the second controllable motor ...
PUM
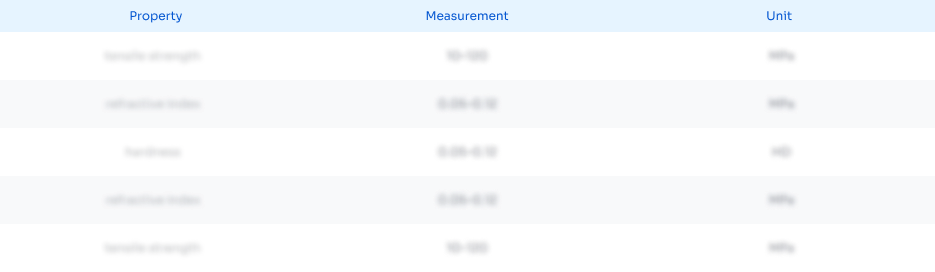
Abstract
Description
Claims
Application Information

- R&D
- Intellectual Property
- Life Sciences
- Materials
- Tech Scout
- Unparalleled Data Quality
- Higher Quality Content
- 60% Fewer Hallucinations
Browse by: Latest US Patents, China's latest patents, Technical Efficacy Thesaurus, Application Domain, Technology Topic, Popular Technical Reports.
© 2025 PatSnap. All rights reserved.Legal|Privacy policy|Modern Slavery Act Transparency Statement|Sitemap|About US| Contact US: help@patsnap.com