Workpiece clamping mechanism
A clamping mechanism and workpiece clamping technology, which is applied in the direction of manufacturing tools, electric processing equipment, metal processing equipment, etc., can solve the problems of high work intensity, affecting processing efficiency, and cannot be fixed, and achieve high repositioning accuracy, simple structure, Strong clamping effect
- Summary
- Abstract
- Description
- Claims
- Application Information
AI Technical Summary
Problems solved by technology
Method used
Image
Examples
Embodiment 1
[0015] Such as Figure 1 to Figure 2 As shown, the workpiece clamping mechanism includes a support plate 3, an elastic member 4, a support cylinder 1 with an open upper end and a closed lower end, and a positioning cylinder 2 coaxially arranged with the support cylinder 1 and having openings at both ends of the upper and lower ends; the support plate 3 is located in the support cylinder 1, the support plate 3 is provided with a first port 7, the center line of the first port 7 overlaps with the axis of the support cylinder 1, and the upper and lower ends of the elastic member 4 are respectively connected to the lower end surface of the support plate 3 and the support cylinder. The bottom of the inner wall of 1 is fixed, and the positioning cylinder 2 is set outside the support cylinder 1. The upper end of the positioning cylinder 2 is provided with a plurality of jaws 5 for positioning the apex of the workpiece. The inner surface of the jaws 5 gradually moves toward the positio...
Embodiment 2
[0019] This embodiment makes the following further limitations on the basis of Embodiment 1: the lower end surface of the support plate 3 is fixedly connected with the limit cylinder 6 which guides the support plate 3 and is arranged coaxially with the support cylinder 1, the limit cylinder 6 The lower end is located in the support cylinder 1. In this embodiment, the upper end of the elastic member 4 can be located in the limiting cylinder 6 . In order to achieve a good and stable guiding function, the outer wall of the limiting cylinder 6 and the inner wall of the supporting cylinder 1 should fit as closely as possible and it should also be ensured that the limiting cylinder 6 can move up and down relative to the supporting cylinder 1 .
Embodiment 3
[0021] In this embodiment, the following further limitations are made on the basis of Embodiment 1: the positioning cylinder 2 and the support cylinder 1 are threaded. In this embodiment, the inner wall of the positioning cylinder 2 may be provided with internal threads, the outer wall of the support cylinder 1 may be provided with external threads matching the internal threads, and the positioning cylinder 2 is sleeved on the support cylinder 1 through threads. In application, if the thickness of the workpiece is large, the positioning cylinder 2 can be rotated to move upward relative to the support cylinder 1; if the thickness of the workpiece is small, the operation is reversed.
PUM
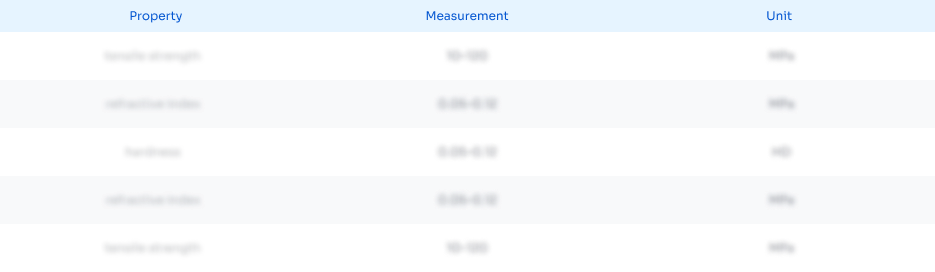
Abstract
Description
Claims
Application Information

- R&D Engineer
- R&D Manager
- IP Professional
- Industry Leading Data Capabilities
- Powerful AI technology
- Patent DNA Extraction
Browse by: Latest US Patents, China's latest patents, Technical Efficacy Thesaurus, Application Domain, Technology Topic, Popular Technical Reports.
© 2024 PatSnap. All rights reserved.Legal|Privacy policy|Modern Slavery Act Transparency Statement|Sitemap|About US| Contact US: help@patsnap.com