Pipe fitting cold extruding forming machine and forming technology thereof
A cold extrusion and forming machine technology, applied in the field of pipe fittings processing, can solve the problems of high labor intensity of workers, increased product cost, unsightly products, etc., and achieves the effect of reducing labor intensity of workers, reducing weight, and forming beautiful shapes.
- Summary
- Abstract
- Description
- Claims
- Application Information
AI Technical Summary
Problems solved by technology
Method used
Image
Examples
Embodiment 1
[0034] Embodiment 1: as Figure 1-Figure 4 As shown, a cold extrusion molding machine for pipe fittings of the present invention includes a frame 3 and a clamping cylinder 1 placed in the frame 3, an ejection cylinder 12, a propulsion cylinder 6, an auxiliary cylinder, and a water injection device. The middle part of the frame 3 is The working platform 13 is transparent, and the ejection cylinder 12 is set in the frame 3 below the working platform 13, and the mold clamping cylinder 1 is set in the corresponding upper frame 3, and the pushing cylinder 6, the mold clamping cylinder 1 and the pushing cylinder 1 are respectively set in the frames 3 on both sides of the working platform 13. The oil cylinders 6 are respectively provided with auxiliary oil cylinders. During work, the workpiece lower mold 9 is placed on the work platform 13, the clamping cylinder 1 is connected with the workpiece upper mold 5, and the two propulsion cylinders 6 are respectively connected with a water i...
Embodiment 2
[0055] Embodiment 2: The difference between this example and Embodiment 1 is that in this example, multiple molds are placed on the working platform 13 in the frame 3 at the same time, and a clamping cylinder 1 and two first auxiliary cylinders 2 are set, corresponding to each workpiece Two propulsion oil cylinders 6 and four second auxiliary oil cylinders 7 are set and extruded at the same time. Improve work efficiency.
PUM
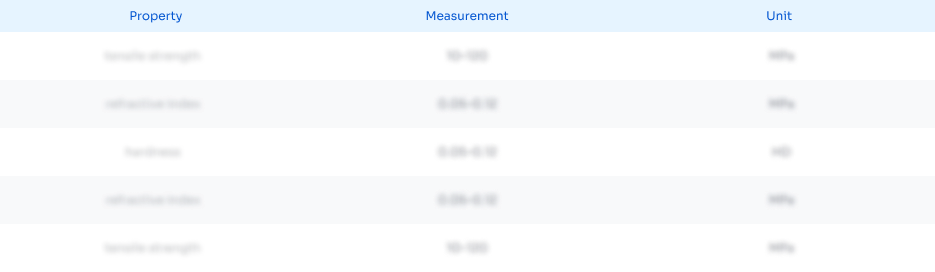
Abstract
Description
Claims
Application Information

- Generate Ideas
- Intellectual Property
- Life Sciences
- Materials
- Tech Scout
- Unparalleled Data Quality
- Higher Quality Content
- 60% Fewer Hallucinations
Browse by: Latest US Patents, China's latest patents, Technical Efficacy Thesaurus, Application Domain, Technology Topic, Popular Technical Reports.
© 2025 PatSnap. All rights reserved.Legal|Privacy policy|Modern Slavery Act Transparency Statement|Sitemap|About US| Contact US: help@patsnap.com