A preparation method and application of paper-making reconstituted tobacco leaf filler
A technology of reconstituted tobacco leaves and papermaking method, which is applied in the field of calcium carbonate surface coating technology to improve the calcium carbonate retention rate of reconstituted tobacco leaves based on papermaking method, to achieve the effect of improving physical and chemical properties, high application value and increasing strength
- Summary
- Abstract
- Description
- Claims
- Application Information
AI Technical Summary
Problems solved by technology
Method used
Image
Examples
Embodiment 1
[0024] Prepare 500mL of calcium chloride solution with a calcium ion concentration of 0.2mol / L and transfer it to a gas washing bottle, weigh 25.0g of light calcium carbonate and add it to the washing bottle, stir evenly, and introduce carbon dioxide gas at a flow rate of 5L / Min, under the condition of 25°C, react for 1 hour, suction filter and dry the obtained light calcium carbonate dispersion, and use the dried coated calcium carbonate as filler to prepare reconstituted tobacco leaf base.
[0025] The preparation method of the reconstituted tobacco leaf base is to prepare the slurry with the dry mass ratio of wood pulp fiber, tobacco stem fiber and shredded fiber at 18:48:29, control the degree of beating to 28°SR, and add the mass at the same time as the dry pulp mass 18% of the filler, and adjust the concentration of the slurry to a mass concentration of 3% of the dry pulp, and then make a reconstituted tobacco leaf base, dry the base, and set aside.
[0026] The calcium...
Embodiment 2
[0028] Prepare 500mL of calcium lactate solution with a calcium ion concentration of 0.25mol / L and transfer it to the gas washing bottle, weigh 37.5g of heavy calcium carbonate and add it to the gas washing bottle, stir evenly, and introduce carbon dioxide gas, the flow rate of carbon dioxide is 10L / min , reacted for 0.5 h at 45° C., suction-filtered and dried the obtained heavy calcium carbonate dispersion, and used the dried coated calcium carbonate as a filler to prepare a reconstituted tobacco leaf base.
[0029] The preparation method of the reconstituted tobacco leaf base is to prepare a slurry with wood pulp fibers, tobacco stem fibers and shredded fibers at an absolute dry mass ratio of 22: 52: 31, control the degree of beating to 32 ° SR, and add the mass to the absolute dry pulp mass 21% of the filler, and adjust the concentration of the slurry to a mass concentration of 3% of the dry pulp, and then make a reconstituted tobacco leaf base, dry the base, and set aside. ...
Embodiment 3
[0032] Prepare 500mL of calcium formate solution with a calcium ion concentration of 0.22mol / L and transfer it to a gas washing bottle, weigh 44.0g of food-grade light calcium carbonate and add it to the washing bottle, stir evenly, and inject carbon dioxide gas, the flow rate of carbon dioxide is 6L / min, under the condition of 30°C, react for 0.7h, suction filter and dry the obtained light calcium carbonate dispersion, and use the dried coated calcium carbonate as filler to prepare reconstituted tobacco leaf base.
[0033] The preparation method of the reconstituted tobacco leaf base is to prepare the slurry with the dry mass ratio of wood pulp fiber, tobacco stem fiber and shredded fiber at 19:51:30, control the degree of beating to 31°SR, and add the mass at the same time as the dry pulp mass 19% of the filler, and adjust the concentration of the slurry to a mass concentration of 3% of the dry pulp, and then make a reconstituted tobacco leaf base, dry the base, and set asid...
PUM
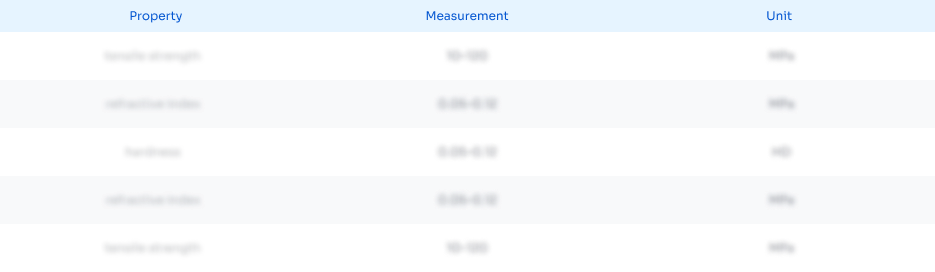
Abstract
Description
Claims
Application Information

- R&D
- Intellectual Property
- Life Sciences
- Materials
- Tech Scout
- Unparalleled Data Quality
- Higher Quality Content
- 60% Fewer Hallucinations
Browse by: Latest US Patents, China's latest patents, Technical Efficacy Thesaurus, Application Domain, Technology Topic, Popular Technical Reports.
© 2025 PatSnap. All rights reserved.Legal|Privacy policy|Modern Slavery Act Transparency Statement|Sitemap|About US| Contact US: help@patsnap.com