ZSM-48/Silicalite-1 composite molecular sieve and preparation method thereof
A technology of ZSM-48 and composite molecular sieve, which is applied in the direction of crystalline aluminosilicate zeolite, etc., can solve the problems of expensive hexamethylenediamine chloride, easy carbon deposition, unfavorable long-term operation of catalyst, etc., achieve suitable pore volume, improve acid Quantity, the effect of inhibiting side effects
- Summary
- Abstract
- Description
- Claims
- Application Information
AI Technical Summary
Problems solved by technology
Method used
Image
Examples
Embodiment 1
[0024] Weigh sodium hydroxide and sodium aluminate (Al 2 o 3 , 43wt%; Na 2 O, 38wt%) was dissolved in deionized water, and then the templating agent R (12-crown-4, content >97%) was added while stirring at a water bath temperature of 60°C, and after stirring for 0.5 hours, white carbon black was added, After stirring for 1 hour, add ZSM-48 seed crystal S, continue stirring for 2 hours, and then move to a closed stainless steel reaction kettle. Crystallized at 160°C for 6 days to obtain ZSM-48 molecular sieve with low silicon-aluminum ratio (D1-ZSM-48). See Table 1 for the specific raw material ratio and product properties.
Embodiment 2
[0026] Weigh sodium hydroxide and sodium aluminate (Al 2 o 3 , 43wt%; Na 2 O, 38wt%) was dissolved in deionized water, and then the templating agent R (12-crown-4, content >97%) was added while stirring at a water bath temperature of 60°C, and after stirring for 0.5 hours, white carbon black was added, After stirring for 1 hour, add ZSM-48 seed crystal S, continue stirring for 2 hours, and then move to a closed stainless steel reaction kettle. Crystallized at 158°C for 8 days to obtain a ZSM-48 molecular sieve (D2-ZSM-48) with a low silicon-aluminum ratio. The specific raw material ratio and product properties are shown in Table 1.
Embodiment 3
[0028] Weigh sodium hydroxide and TPABr and dissolve them in deionized water, then add D1-ZSM-48 molecular sieve while stirring at room temperature, stir for 0.5 hours, then add white carbon black, stir for 0.5 hours, then move the reaction mixture gel to an airtight In a stainless steel reaction kettle, crystallize at 140°C for 12 hours, and the crystallized product is washed, centrifuged, dried, and roasted to obtain ZSM-48 / Silicalite-1 composite molecular sieve. The specific raw material ratio and product properties are shown in Table 2.
PUM
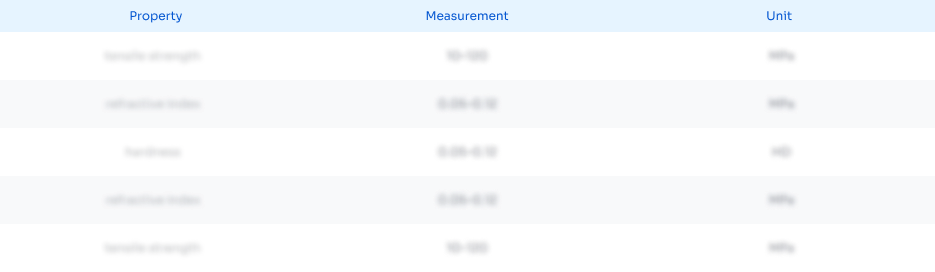
Abstract
Description
Claims
Application Information

- R&D
- Intellectual Property
- Life Sciences
- Materials
- Tech Scout
- Unparalleled Data Quality
- Higher Quality Content
- 60% Fewer Hallucinations
Browse by: Latest US Patents, China's latest patents, Technical Efficacy Thesaurus, Application Domain, Technology Topic, Popular Technical Reports.
© 2025 PatSnap. All rights reserved.Legal|Privacy policy|Modern Slavery Act Transparency Statement|Sitemap|About US| Contact US: help@patsnap.com