Preparation method for enhanced heat transfer type nano-refrigerant
A kind of refrigerant and nanotechnology, which is applied in the field of preparation of heat transfer-enhanced nano-refrigerants, can solve the problems of affecting the heat transfer performance of refrigerants, the influence of two-phase mixing degree, increasing equipment investment and energy consumption, and achieving heat transfer performance Excellent, low cost, and improved thermal conductivity
- Summary
- Abstract
- Description
- Claims
- Application Information
AI Technical Summary
Problems solved by technology
Method used
Image
Examples
Embodiment 1
[0024] Step 1: Nano-gadolinium oxide surface polymerization
[0025] According to 1g per serving, the polymerization ratio is as follows:
[0026]
[0027] According to the proportion of nano oxide gadolinium Disperse in ethanol, then add trifluoroethyl acrylate monomer, benzoyl peroxide, polyvinyl alcohol, sodium dodecylbenzenesulfonate, heat up, and react at 70°C for 9 hours to obtain surface-polymerized nano oxidationgadolinium Microsuspension.
[0028] Step 2: Blending
[0029] 0.008Kg step (1) prepares the nano-oxidized gadolinium Microsuspension with 98.3Kg 2,3,3,3-tetrafluoropropene (HFO1234yf), 1.6912Kg 1,2,3,3,3-pentafluoropropene (HFO-1225ye), 0.0008Kg 1-allyl-3- Methylimidazole hexafluorophosphate was pre-mixed in a 500L stirred reactor for 20h, and then added to a high-throughput microchannel glass reactor (produced by Corning Corporation of the United States, GEN-1 type), and passed through a sufficient flow rate of 10Kg / h Mix to obtain the product. The n...
Embodiment 2
[0031] Step 1: Nanooxidation gadolinium surface aggregation
[0032] According to 1g per serving, the polymerization ratio is as follows:
[0033]
[0034] Disperse nano-gadolinium oxide in ethanol according to the ratio, then add trifluoroethyl acrylate monomer, benzoyl peroxide, polyvinyl alcohol, sodium dodecylbenzenesulfonate, heat up, and react at 60°C for 15 hours, that is nano-oxidized gadolinium Microsuspension.
[0035] Step 2: Blending
[0036] 0.01Kg surface polymerized nano oxide gadolinium Microsuspension with 600Kg HFO1234yf, 399.985KgHFO-1225ye, 0.005Kg 1-allyl-3-methylimidazole hexafluorophosphate in 2m 3 Pre-mixed in a stirred reactor for 10 hours, then added to a high-throughput microchannel glass reactor (manufactured by Corning Corporation of the United States, GEN-2 type), and fully mixed at a flow rate of 40Kg / h to obtain the product, numbered as WN-2 .
Embodiment 3
[0038] Step 1: Nano-gadolinium oxide surface polymerization
[0039] According to 1g per serving, the polymerization ratio is as follows:
[0040]
[0041] Disperse nano-gadolinium oxide in ethanol according to the proportion, then add trifluoroethyl acrylate monomer, benzoyl peroxide, polyvinyl alcohol, sodium dodecylbenzenesulfonate, etc., heat up, and react at 80°C for 6 hours. nano oxide gadolinium Microsuspension.
[0042] Step 2: Blending
[0043] 0.1Kg surface polymerized nano oxide gadolinium Microsuspension with 800Kg HFO1234yf, 199.87Kg HFO-1225ye, 0.03Kg 1-allyl-3-methylimidazole hexafluorophosphate in 2m 3 Pre-mixed in a stirred reactor for 35 hours, then added to a high-throughput microchannel glass reactor (produced by Corning Corporation of the United States, GEN-3 type), and fully mixed at a flow rate of 100Kg / h to obtain a product number of WN-3.
PUM
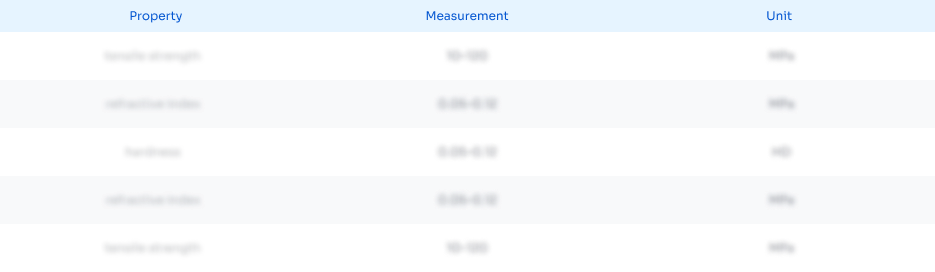
Abstract
Description
Claims
Application Information

- R&D Engineer
- R&D Manager
- IP Professional
- Industry Leading Data Capabilities
- Powerful AI technology
- Patent DNA Extraction
Browse by: Latest US Patents, China's latest patents, Technical Efficacy Thesaurus, Application Domain, Technology Topic, Popular Technical Reports.
© 2024 PatSnap. All rights reserved.Legal|Privacy policy|Modern Slavery Act Transparency Statement|Sitemap|About US| Contact US: help@patsnap.com