Cement bin and manufacturing process thereof
A cement silo and cone technology, applied in the field of machinery, can solve the problems of long production cycle of the silo, waste of solder resources, harsh working environment, etc., to achieve the improvement of processing accuracy and product quality and aesthetics, shorten the production cycle, realize normalized effect
- Summary
- Abstract
- Description
- Claims
- Application Information
AI Technical Summary
Problems solved by technology
Method used
Image
Examples
Embodiment 1
[0026] like figure 1 and Figure 4 Commonly shown, the cement silo, from top to bottom, includes an upper cone 1, a middle cylinder 2 and a lower cone 3 connected by fasteners; the upper cone 1 includes several upper cone splicing modules 4 of the same size , several upper cone splicing modules 4 are assembled to form the upper cone 1; the middle cylinder 2 includes several intermediate cylinder splicing modules 5 of the same size, and several intermediate cylinder splicing modules 5 are assembled to form the middle cylinder 2; the lower cone 3 Including an end cone 6 and at least one conical cylinder 7, the conical cylinder 7 and the end cone 6 are installed together by fasteners, the conical cylinder 7 includes several conical cylinder splicing modules 8, several conical cylinder splicing modules 8 is assembled to form a conical cylinder 7, and each conical cylinder splicing module 8 includes a conical cylinder splicing module body 9, and the left and right sides of the con...
Embodiment 2
[0034] The manufacturing process of the cement silo includes the following steps:
[0035] step one
[0036] Make the upper cone splicing module 4; cut out some trapezoidal metal plates required for making the upper cone splicing module 4 with a numerical control machine tool, and use a drilling mold to carry out the trapezoidal metal plates required for the upper cone splicing module 4 on the left and right sides. Drill holes, then use the upper cone splicing module stamping die to bend the trapezoidal metal sheet into an arc shape through a hydraulic press, and punch out strip flanges on both sides of the metal sheet, and then fix the strip flanges on both sides, The lower end of the metal plate is welded with arc-shaped flanges, and finally the two shaped flanges are loosened, and the manufacture of an upper cone splicing module 4 is completed.
[0037] step two
[0038] Make the intermediate cylinder splicing module 5; cut out a number of rectangular metal plates require...
PUM
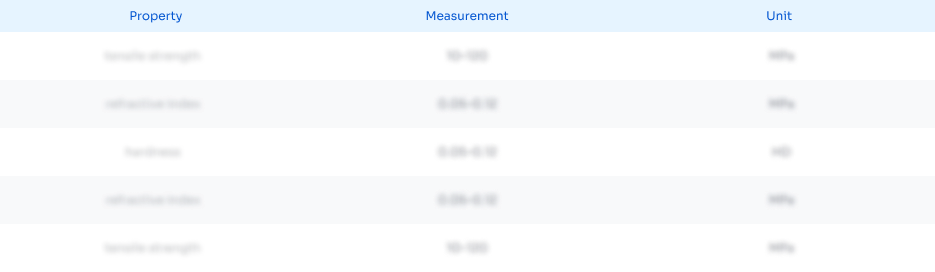
Abstract
Description
Claims
Application Information

- Generate Ideas
- Intellectual Property
- Life Sciences
- Materials
- Tech Scout
- Unparalleled Data Quality
- Higher Quality Content
- 60% Fewer Hallucinations
Browse by: Latest US Patents, China's latest patents, Technical Efficacy Thesaurus, Application Domain, Technology Topic, Popular Technical Reports.
© 2025 PatSnap. All rights reserved.Legal|Privacy policy|Modern Slavery Act Transparency Statement|Sitemap|About US| Contact US: help@patsnap.com