Production method of manganese-zinc ferrite magnetic core
A technology of manganese zinc ferrite and production method, which is applied in the direction of inorganic material magnetism, inductance/transformer/magnet manufacturing, circuit, etc., can solve the problem of poor quality of manganese zinc ferrite core, unreasonable production method and low production efficiency Low-level problems, to achieve the effect of improving the efficiency of green body placement, increasing the loading capacity, and stabilizing product performance
- Summary
- Abstract
- Description
- Claims
- Application Information
AI Technical Summary
Problems solved by technology
Method used
Image
Examples
Embodiment 1
[0041] This embodiment discloses a production method of a manganese zinc ferrite core, such as figure 1 As shown, the following steps are included: compacting, swinging, sintering heating, sintering heat preservation and sintering cooling, wherein:
[0042] The compact is pressed by conventional pressing equipment, and the components and mass proportions of the green compact are 70% of ferric oxide, 22.4% of manganese oxide, and 7.6% of zinc oxide.
[0043] In this embodiment, the pressed green bodies are automatically stacked and placed in the setter plate through the automatic billet placement machine; the automatic billet placement machine includes: a transmission unit, a pneumatic billet push unit, a workbench and a green body adsorption and placement unit , the feeding end of the transfer unit is connected to the discharge end of the compacting equipment, and the lower end of the transfer unit is provided with a pneumatic push unit capable of pushing the green body to the...
Embodiment 2
[0058] This embodiment discloses a production method of a manganese-zinc ferrite core, which includes the following steps: compacting, laying the blank, sintering temperature rise, sintering heat preservation and sintering temperature reduction, wherein:
[0059] The compact is pressed by conventional pressing equipment, and the components and mass proportions of the green compact are 70% of ferric oxide, 22.4% of manganese oxide, and 7.6% of zinc oxide. The blanks are automatically stacked and placed in the setter plate through an automatic blanking machine. The automatic blanking machine used in this embodiment is the same as that in Example 1;
[0060] Described sintering heating up is subsection heating up, is respectively:
[0061] (1.1) Raise the green body from room temperature to 700°C to remove the binder and moisture in the green body, the heating rate is 2°C / min, and keep it at 450°C for 2 hours, gradually strengthen the ventilation, and force the air flow From 10....
Embodiment 3
[0071] This embodiment discloses a production method of a manganese-zinc ferrite core, which includes the following steps: compacting, laying the blank, sintering temperature rise, sintering heat preservation and sintering temperature reduction, wherein:
[0072] The compact is pressed by conventional pressing equipment, and the components and mass proportions of the green compact are 70% of ferric oxide, 22.4% of manganese oxide, and 7.6% of zinc oxide.
[0073] The blanks are automatically stacked and placed in the setter plate through an automatic blanking machine. The automatic blanking machine used in this embodiment is the same as that in Example 1;
[0074] Described sintering heating up is subsection heating up, is respectively:
[0075] (1.1) Raise the green body from room temperature to 700°C to remove the binder and moisture in the green body, the heating rate is 1.5°C / min, and keep warm at 400°C for 1.5h, keep ventilation, gradually strengthen ventilation, force I...
PUM
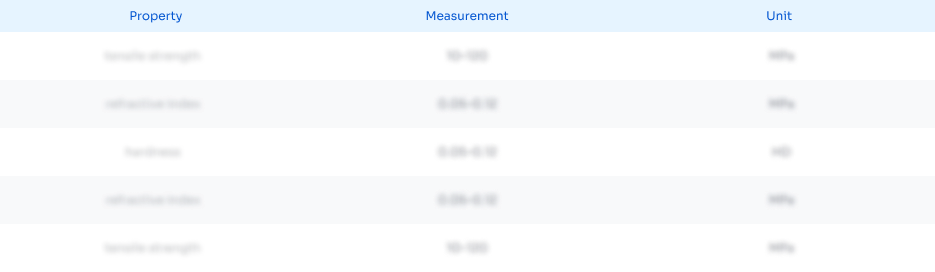
Abstract
Description
Claims
Application Information

- R&D Engineer
- R&D Manager
- IP Professional
- Industry Leading Data Capabilities
- Powerful AI technology
- Patent DNA Extraction
Browse by: Latest US Patents, China's latest patents, Technical Efficacy Thesaurus, Application Domain, Technology Topic, Popular Technical Reports.
© 2024 PatSnap. All rights reserved.Legal|Privacy policy|Modern Slavery Act Transparency Statement|Sitemap|About US| Contact US: help@patsnap.com