Method for preparing sodium fluoride from defluorination residue generated in production of phosphoric acid by wet process
A wet-process phosphoric acid, sodium fluoride technology, applied in the direction of alkali metal fluoride, etc., can solve the problem of difficult separation of sodium fluoride crystals and silica, achieve low silicon content, reduce production costs, reduce water consumption and mother liquor The effect of emissions
- Summary
- Abstract
- Description
- Claims
- Application Information
AI Technical Summary
Problems solved by technology
Method used
Image
Examples
Embodiment 1
[0034] 1) Prepare wet-process phosphoric acid defluorination slag with mother liquor to make a slurry with a specific gravity of 1.18g / ml; use mother liquor for sodium carbonate to prepare a solution with a specific gravity of 1.25g / ml; wet-process phosphoric acid defluorination slag contains P 2 o 5 : 0.52%, fluorine: 38.12%, SO 4 2- : 3.51%, moisture: 22.12%.
[0035] 2) The defluorinated slag slurry and sodium carbonate solution prepared in step 1) were respectively mixed with 0.70m 3 / h, 0.48m 3 The flow rate of / h is continuously added to the reaction crystallization tank, and the slurry containing fine sodium fluoride crystals obtained by centrifugation in step 4) is fed at a temperature of 1.85 m 3 / h into the reaction crystallization tank, the reaction decomposes and forms a slurry containing coarse particles of sodium fluoride crystals. The temperature in the tank is controlled at 90±5°C, the residence time of the material reaction is 4.5 hours, and the stirring ...
Embodiment 2
[0040] 1) The wet-process phosphoric acid defluorination slag is prepared into a slurry with a specific gravity of 1.23g / ml with the mother liquor; sodium carbonate is prepared with a mother liquor with a specific gravity of 1.27g / ml; the wet-process phosphoric acid defluorination slag contains P 2 o 5 : 0.46%, fluorine: 38.55%, SO 4 2- : 3.11%, moisture: 24.62%.
[0041] 2) The defluorinated slag slurry and sodium carbonate solution prepared in step 1) were respectively mixed with 0.75m 3 / h, 0.51m 3 The flow rate of / h is continuously added to the reaction crystallization tank, and the slurry containing fine sodium fluoride crystals obtained by step 4) is centrifuged at 1.75m 3 / h into the reaction crystallization tank, the reaction decomposes and forms a slurry containing coarse particles of sodium fluoride crystals. The temperature in the tank is controlled at 90±5°C, the residence time of the material reaction is 5.0 hours, and the stirring linear velocity in the tan...
Embodiment 3
[0046] 1) The wet-process phosphoric acid defluorination slag is prepared into a slurry with a specific gravity of 1.25g / ml with the mother liquor; sodium carbonate is prepared with a mother liquor with a specific gravity of a solution with a specific gravity of 1.30g / ml; the wet-process phosphoric acid defluorination slag contains P2O5: 0.55%, Fluorine: 38.42%, SO 4 2- : 3.28%, moisture: 23.75%.
[0047] 2) The defluorinated slag slurry and sodium carbonate solution prepared in step 1) were respectively mixed with 0.85m 3 / h, 0.53m 3 The flow rate of / h is continuously added to the reaction crystallization tank, and simultaneously the slurry containing fine sodium fluoride crystals obtained by screening and centrifugation in step 4) is 1.80m 3 / h into the reaction crystallization tank, the reaction decomposes and forms a slurry containing coarse particles of sodium fluoride crystals. The temperature in the tank is controlled at 90±5°C, the residence time of the material r...
PUM
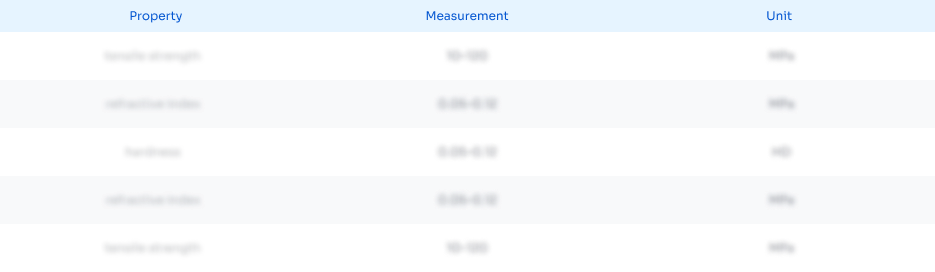
Abstract
Description
Claims
Application Information

- Generate Ideas
- Intellectual Property
- Life Sciences
- Materials
- Tech Scout
- Unparalleled Data Quality
- Higher Quality Content
- 60% Fewer Hallucinations
Browse by: Latest US Patents, China's latest patents, Technical Efficacy Thesaurus, Application Domain, Technology Topic, Popular Technical Reports.
© 2025 PatSnap. All rights reserved.Legal|Privacy policy|Modern Slavery Act Transparency Statement|Sitemap|About US| Contact US: help@patsnap.com