Normal alignment method based on parallel mechanism
A parallel, end-effector technology, used in metal processing machinery parts, metal processing, automatic control devices, etc., can solve the problems of difficult adjustment, complex calculation process, limited adjustment range, etc., to meet the requirements of hole-making accuracy, inverse solution Simple algorithm and accurate normal alignment effect
- Summary
- Abstract
- Description
- Claims
- Application Information
AI Technical Summary
Problems solved by technology
Method used
Image
Examples
Embodiment Construction
[0023] The present invention will be described in further detail below in conjunction with the accompanying drawings.
[0024] The device used in the normal alignment method based on the parallel mechanism of the present invention includes a parallel mechanism, a cross slide, four laser displacement sensors and an end effector, and the whole device is controlled and adjusted by a drilling riveting system controller. The above-mentioned parallel mechanism has two degrees of freedom of rotation, including a fixed platform and a moving platform. The fixed platform and the moving platform are connected by two telescopic rods and a fixed rod. The movable platform is connected, the telescopic rod is connected with the fixed platform through the spherical pair, the fixed rod is fixedly connected with the fixed platform, and its branch chain constitutes the SPU structure. Four laser displacement sensors are installed on the end effector, and the end effector is installed on the moving...
PUM
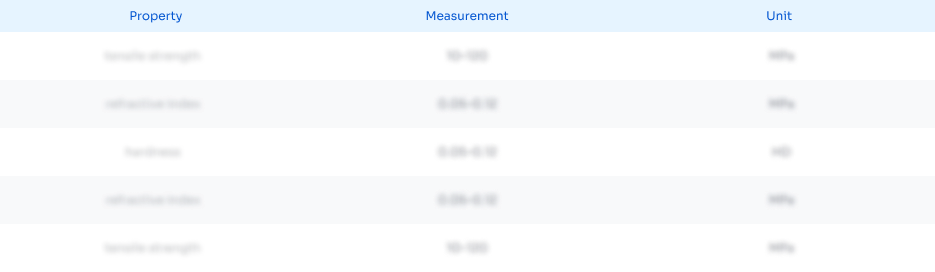
Abstract
Description
Claims
Application Information

- Generate Ideas
- Intellectual Property
- Life Sciences
- Materials
- Tech Scout
- Unparalleled Data Quality
- Higher Quality Content
- 60% Fewer Hallucinations
Browse by: Latest US Patents, China's latest patents, Technical Efficacy Thesaurus, Application Domain, Technology Topic, Popular Technical Reports.
© 2025 PatSnap. All rights reserved.Legal|Privacy policy|Modern Slavery Act Transparency Statement|Sitemap|About US| Contact US: help@patsnap.com