Parallel controllable drilling robot mechanism
A mechanical and robotic technology, applied in the direction of program-controlled manipulators, drilling/drilling equipment, manipulators, etc., can solve the problems of heavy arm weight, heavy weight, poor dynamic performance of the mechanism, etc., and achieve good dynamic performance and rigidity The effect of large weight ratio and strong load capacity
- Summary
- Abstract
- Description
- Claims
- Application Information
AI Technical Summary
Problems solved by technology
Method used
Image
Examples
Embodiment Construction
[0029] The technical solutions of the present invention will be further described below in conjunction with the accompanying drawings and embodiments.
[0030] control figure 1 , 7 , 8 and 9, a parallel controllable mechanism type drilling robot mechanism, including a central branch chain with a closed-loop sub-chain, four controllable adjustment branch chains, a moving platform 13 with a flange 15, a frame 2 and a rotary Platform 1. The frame 2 is installed on the rotary platform 1 to realize the flexible and changeable working requirements of the whole robot mechanism in the working space.
[0031] control figure 1 , 2 , the first controllable adjustment branch chain is composed of the first active rod 6 and the first connecting rod 10 . One end of the first active rod 6 is connected to the frame 2 through the first rotating pair 3 , and the other end is connected to the first connecting rod 10 through the first Hooke hinge 7 . The other end of the first connecting rod...
PUM
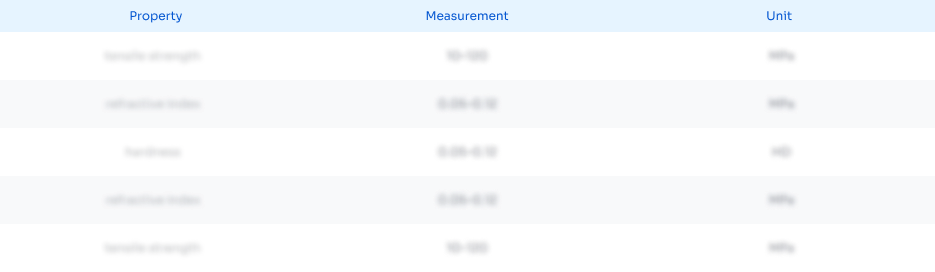
Abstract
Description
Claims
Application Information

- Generate Ideas
- Intellectual Property
- Life Sciences
- Materials
- Tech Scout
- Unparalleled Data Quality
- Higher Quality Content
- 60% Fewer Hallucinations
Browse by: Latest US Patents, China's latest patents, Technical Efficacy Thesaurus, Application Domain, Technology Topic, Popular Technical Reports.
© 2025 PatSnap. All rights reserved.Legal|Privacy policy|Modern Slavery Act Transparency Statement|Sitemap|About US| Contact US: help@patsnap.com