Automatic continuous forming mold of automobile armrest framework
A technology for automobile armrests and forming molds, which is applied in the direction of forming tools, manufacturing tools, vehicle parts, etc., and can solve problems that affect product processing accuracy and product production efficiency
- Summary
- Abstract
- Description
- Claims
- Application Information
AI Technical Summary
Problems solved by technology
Method used
Image
Examples
Embodiment Construction
[0022] Such as Figure 1 to Figure 4The automatic continuous molding mold for the skeleton of the automobile handrail includes an upper mold assembly and a lower mold assembly, and the upper mold assembly and the lower mold assembly are continuous molds. The lower mold assembly has a lower mold base 1, and the four corners of the lower mold base 1 are respectively connected with first guide pillars 2, and the first guide pillars 2 are ball guide pillars; the lower backing plate 42 is located above the lower mold base 1, The lower mold connecting plate 43 is located above the lower backing plate 42; on the lower mold connecting plate 43, eight steel plate guide columns 3 symmetrically located on both sides of the central axis of the lower mold connecting plate 43 are connected, and the steel plate guide columns 3 are arranged on the cylindrical surface of the lower mold connecting plate 43. An annular groove is provided; on the lower die connecting plate 43, there are also eigh...
PUM
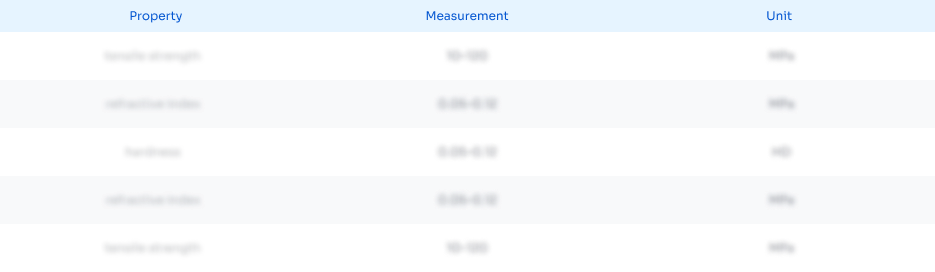
Abstract
Description
Claims
Application Information

- R&D
- Intellectual Property
- Life Sciences
- Materials
- Tech Scout
- Unparalleled Data Quality
- Higher Quality Content
- 60% Fewer Hallucinations
Browse by: Latest US Patents, China's latest patents, Technical Efficacy Thesaurus, Application Domain, Technology Topic, Popular Technical Reports.
© 2025 PatSnap. All rights reserved.Legal|Privacy policy|Modern Slavery Act Transparency Statement|Sitemap|About US| Contact US: help@patsnap.com