A vibration energy control system and method
A vibration energy and control system technology, applied in the direction of control of mechanical energy, electric components, gas-hydraulic dampers, etc., can solve problems such as poor vibration control effect and energy waste
- Summary
- Abstract
- Description
- Claims
- Application Information
AI Technical Summary
Problems solved by technology
Method used
Image
Examples
Embodiment 1
[0075] see figure 1 , which shows a schematic structural view of a vibration energy control system provided by the present invention, including: an upper connection head 100, a lower connection head 200, and a vibration system 300, wherein the vibration system 300 specifically includes: a piston rod 301, Compressed gas 302, hydraulic oil 303, piston 304, piston overflow valve 305, piston check valve 306, inner cylinder check valve 307, inner cylinder 308 and outer cylinder 309.
[0076] Specifically in this embodiment, the upper connector 100 is connected to one end of the piston rod 301, the other end of the piston rod 301 is equipped with a piston 304, and the piston overflow valve 305 and the piston check valve 306 are arranged on the piston 304; The valve 307 is installed at the bottom of the inner cylinder 308; the outer cylinder 309 is concentrically installed on the outside of the inner cylinder 308; the outer cylinder 309 is connected with the lower connector 200; hydr...
Embodiment 2
[0114] Based on the above examples, please refer to image 3 , which shows another structural schematic diagram of a vibration energy control system provided by the present invention, which also includes: a rectifier 1000 electrically connected to the generator motor 500, and an energy consumption resistor 1100 connected in series with the rectifier 1000. Wherein, the MCU 900 is also connected to the rectifier 1000 .
[0115] At this time, the MCU 900 is used to control and adjust the control angle of the bidirectional converter 600 when the current vibration force generated by the vibration system 300 is greater than the maximum generating damping force under the joint action of the battery 700 and the energy dissipation resistor 1100, so that the control angle of the bidirectional converter 600 is Driven by electric energy, the generator motor 500 is controlled to generate a damping force to offset the vibration force; when the current vibration force generated by the vibrat...
PUM
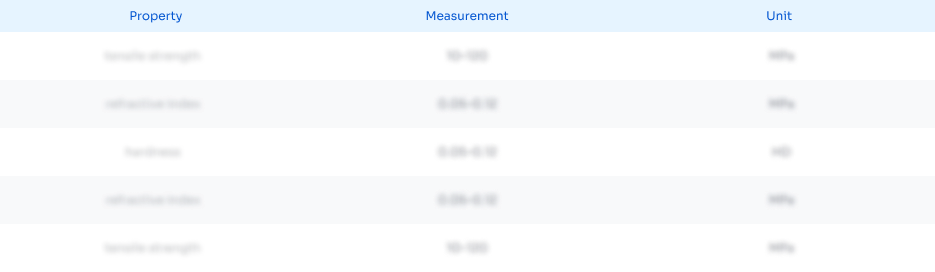
Abstract
Description
Claims
Application Information

- R&D
- Intellectual Property
- Life Sciences
- Materials
- Tech Scout
- Unparalleled Data Quality
- Higher Quality Content
- 60% Fewer Hallucinations
Browse by: Latest US Patents, China's latest patents, Technical Efficacy Thesaurus, Application Domain, Technology Topic, Popular Technical Reports.
© 2025 PatSnap. All rights reserved.Legal|Privacy policy|Modern Slavery Act Transparency Statement|Sitemap|About US| Contact US: help@patsnap.com