Assembly system and assembly method for press-mounted bushing
An assembly system and press-fitting device technology, applied in metal processing, metal processing equipment, manufacturing tools, etc., can solve the problems of poor installation accuracy, high production cost, and low installation efficiency of camshaft bushings, and achieve high assembly efficiency, The effect of high assembly precision
- Summary
- Abstract
- Description
- Claims
- Application Information
AI Technical Summary
Problems solved by technology
Method used
Image
Examples
Embodiment Construction
[0057] The invention is an assembly system that can be used for press-fitting the bushing, and is suitable for the bushing assembly of the engine body whose camshaft hole and the inner hole diameter of the bushing are arranged in increasing (or decreasing) arrangement. The assembly method is to install bushings on the second pressure head guide device and the first pressure head guide device, and guide the second pressure head guide device through the second servo press installation device and the first servo press installation device. and the bushing on the first pressure head guide device are press-fitted into the engine body.
[0058] The preferred embodiments of the present invention are given below in conjunction with the accompanying drawings to describe the technical solution of the present invention in detail.
[0059] Such as figure 1 As shown, the assembly system for press-fitting bushings of the present invention includes an installation platform 1 on which an engi...
PUM
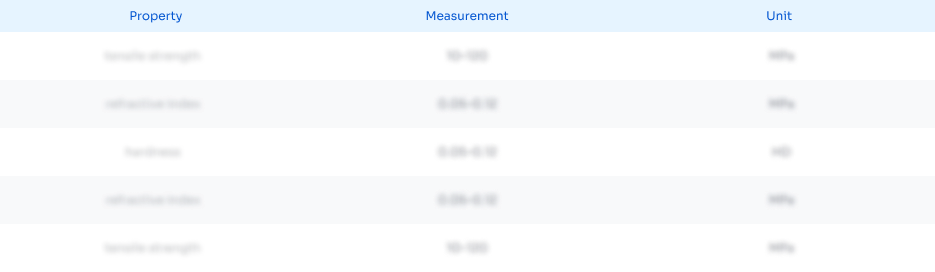
Abstract
Description
Claims
Application Information

- R&D
- Intellectual Property
- Life Sciences
- Materials
- Tech Scout
- Unparalleled Data Quality
- Higher Quality Content
- 60% Fewer Hallucinations
Browse by: Latest US Patents, China's latest patents, Technical Efficacy Thesaurus, Application Domain, Technology Topic, Popular Technical Reports.
© 2025 PatSnap. All rights reserved.Legal|Privacy policy|Modern Slavery Act Transparency Statement|Sitemap|About US| Contact US: help@patsnap.com