Trajectory control device for articulated robot, and control method
A multi-joint robot and trajectory control technology, applied in the direction of robot, computer control, program control, etc., can solve the problems of low vibration frequency, trajectory error, and no speed feedforward
- Summary
- Abstract
- Description
- Claims
- Application Information
AI Technical Summary
Problems solved by technology
Method used
Image
Examples
no. 1 Embodiment approach
[0047] [overall composition]
[0048] First, an outline of a vertical articulated robot (hereinafter sometimes simply referred to as an articulated robot) using the trajectory control device according to the present embodiment will be described.
[0049] figure 1 It is an example of a robot that performs a tilting motion (swing motion) of a welding torch, and is a diagram showing an outline of an articulated robot 1 employing a trajectory control device according to this embodiment. The articulated robot 1 is of a vertical articulated type and includes six joints J1 to J6, and performs arc welding with a welding wire fed from a welding torch provided at the tip of the axis of J6. The articulated robot 1 sets a welding operation interval between a predetermined welding start point and a welding end point, moves in the direction of a welding line connecting the welding start point and welding end point, and sets the welding wire so that A tilting motion (swinging motion) is pe...
no. 2 Embodiment approach
[0083] Hereinafter, a trajectory control device according to a second embodiment of the present invention will be described. In addition, the trajectory control device according to the present embodiment is different from the trajectory control device 10 according to the above-mentioned first embodiment in the provision method of the first dynamic characteristic calculation unit 300 . Other than that, it is the same as that of the first embodiment, so the parts that overlap with the above description will not be repeated.
[0084] In the first embodiment described above, the second dynamic characteristic calculation unit 400 is provided with a high-frequency rejection characteristic equal to or greater than that of the first dynamic characteristic calculation unit 300 . In the present embodiment, the second dynamic characteristic calculation unit 400 is provided with a very strong high-frequency blocking characteristic similarly to the first embodiment. In addition, the first...
no. 3 Embodiment approach
[0106] Hereinafter, a trajectory control device according to a third embodiment of the present invention will be described. In addition, the trajectory control device according to the present embodiment is different from the trajectory control device 10 according to the above-mentioned first embodiment in the provision method of the first dynamic characteristic calculation unit 300 . Other than that, it is the same as that of the first embodiment, so the parts that overlap with the above description will not be repeated.
[0107] Since the current control characteristic responds very quickly, considering that good performance can be obtained even if it is close to "gain = 1", Formula (1) can be transformed into the following Formula (5).
[0108] [Formula 5]
[0109] Gp · Gv · s + Gp · Gi J ...
PUM
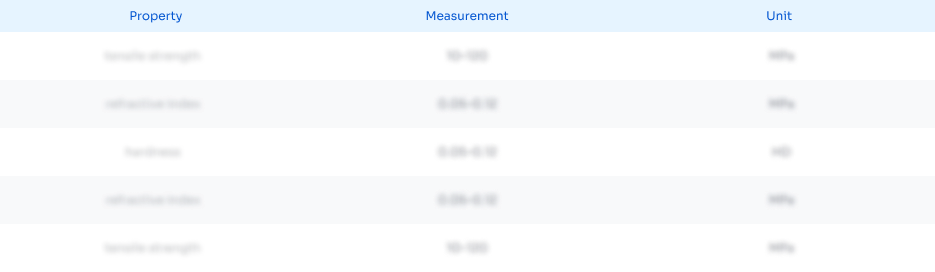
Abstract
Description
Claims
Application Information

- Generate Ideas
- Intellectual Property
- Life Sciences
- Materials
- Tech Scout
- Unparalleled Data Quality
- Higher Quality Content
- 60% Fewer Hallucinations
Browse by: Latest US Patents, China's latest patents, Technical Efficacy Thesaurus, Application Domain, Technology Topic, Popular Technical Reports.
© 2025 PatSnap. All rights reserved.Legal|Privacy policy|Modern Slavery Act Transparency Statement|Sitemap|About US| Contact US: help@patsnap.com