Device and method for adopting electronic reaction beam for making ultrafine metal powder
A technology of ultra-fine metal powder and application of electronics, applied in the field of metal powder processing equipment, can solve the problems of environmental pollution, high energy consumption, application limitations, etc., and achieve the effects of wide application range, energy saving, and energy consumption reduction
- Summary
- Abstract
- Description
- Claims
- Application Information
AI Technical Summary
Problems solved by technology
Method used
Image
Examples
Embodiment Construction
[0026] Below in conjunction with accompanying drawing, the present invention will be further described with specific embodiment, see figure 1 :
[0027] A device for making ultra-fine metal powders by using an electron reaction beam. A crucible 38 is provided in the inner cavity 50 (such as the middle or bottom) of the vacuum evaporation chamber 12, and a crucible 38 is provided on the wall of the vacuum evaporation chamber 12 on the upper side or one side. There is a charging device 18 with discharge valves 15, 16 that can be charged in the crucible 38 and more than one electron gun 14 that makes the metal change from solid to gaseous state, the inner cavity of the vacuum evaporation chamber 12 and the vacuum receiving chamber 28 The inner cavity is communicated through a pipeline with a vacuum valve. The inner cavity 50 of the vacuum receiving chamber 28 and the inner cavity 25 of the vacuum evaporation chamber 12 are connected with a vacuum pumping system controlled by the ...
PUM
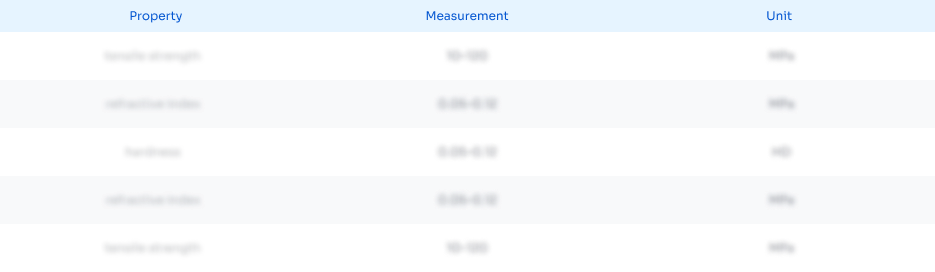
Abstract
Description
Claims
Application Information

- R&D
- Intellectual Property
- Life Sciences
- Materials
- Tech Scout
- Unparalleled Data Quality
- Higher Quality Content
- 60% Fewer Hallucinations
Browse by: Latest US Patents, China's latest patents, Technical Efficacy Thesaurus, Application Domain, Technology Topic, Popular Technical Reports.
© 2025 PatSnap. All rights reserved.Legal|Privacy policy|Modern Slavery Act Transparency Statement|Sitemap|About US| Contact US: help@patsnap.com